Table Of Contents
Category
Artificial Intelligence
AIML
IoT
1. Introduction to AI in Quality Assurance
Artificial Intelligence (AI) is transforming various industries, and Quality Assurance (QA) is no exception. The integration of AI into QA processes, such as ai for qa and ai quality assurance, is enhancing efficiency, accuracy, and overall product quality. This introduction sets the stage for understanding how artificial intelligence assurance is reshaping QA practices and the benefits it brings to organizations.
1.1. What is Quality Assurance and Its Evolution?
Quality Assurance (QA) refers to the systematic processes and activities designed to ensure that products and services meet specified requirements and standards. The primary goal of QA is to prevent defects and ensure quality throughout the development lifecycle.
- Historical Context:
- QA has roots in manufacturing, where it began as a way to inspect products for defects.
- Over time, QA evolved to include processes that focus on prevention rather than detection.
- Key Milestones in QA Evolution:
- The introduction of Total Quality Management (TQM) in the 1980s emphasized continuous improvement.
- The rise of software development in the late 20th century led to the development of software testing methodologies, including ai in quality assurance.
- Agile and DevOps practices in the 21st century have further transformed QA, promoting collaboration and faster delivery.
- Current Trends:
- Automation has become a significant aspect of QA, allowing for more efficient testing processes, such as ai for qa testing.
- The emergence of AI and machine learning for qa is the latest evolution, enabling predictive analytics and smarter testing strategies.
1.2. Traditional QA vs. AI-Powered QA: A Comparative Analysis
The shift from traditional QA methods to AI-powered QA represents a significant change in how quality is managed and assured. Understanding the differences between these two approaches is crucial for organizations looking to enhance their QA processes.
- Traditional QA:
- Relies heavily on manual testing and human intervention, making testing processes often time-consuming and prone to human error.
- Focuses on predefined test cases and scripts, which can limit flexibility.
- Quality metrics are typically gathered post-development, leading to late-stage defect discovery.
- AI-Powered QA:
- Utilizes machine learning algorithms to analyze data and predict potential defects, as seen in ai in qa automation.
- Automates repetitive testing tasks, freeing up human testers for more complex issues.
- Adapts testing strategies based on real-time data and user behavior.
- Enables continuous testing and integration, allowing for immediate feedback and faster release cycles.
- Benefits of AI-Powered QA:
- Increased efficiency through automation reduces testing time and costs.
- Enhanced accuracy by minimizing human error and improving defect detection rates.
- Greater adaptability to changes in requirements or user needs, particularly in qa for ai.
- Predictive analytics can identify potential issues before they arise, leading to proactive quality management, which is essential for quality assurance for ai.
In conclusion, the evolution of QA from traditional methods to AI-powered approaches marks a significant advancement in ensuring product quality. Organizations in production sector embrace ai for quality control and ai in software quality assurance can expect improved efficiency, accuracy, and overall product quality. By partnering with Rapid Innovation, clients can leverage our expertise in AI and Blockchain development to achieve greater ROI, streamline their QA processes, and ultimately deliver superior products to their customers. For more insights on AI agents in software testing, visit this link on AI Agent in Software Testing.
Refer to the image for a visual representation of the evolution of Quality Assurance and the impact of AI on QA processes:
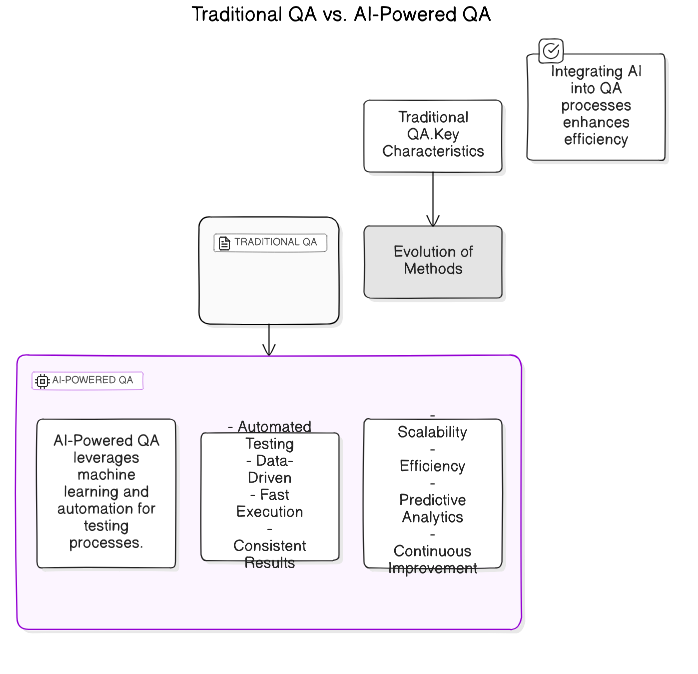
1.3. Building the Business Case for AI in Quality Assurance
- AI can significantly enhance the efficiency and effectiveness of Quality Assurance (QA) processes.
- Key benefits of integrating AI into QA include:
- Improved accuracy in defect detection, reducing the risk of human error.
- Faster testing cycles, allowing for quicker product releases.
- Enhanced predictive analytics, enabling teams to foresee potential issues before they arise.
- Cost savings can be substantial:
- AI can automate repetitive tasks, freeing up human resources for more complex problem-solving.
- According to a report, organizations that implement AI for QA can reduce testing costs by up to 30%.
- AI tools can provide real-time insights and analytics, helping teams make data-driven decisions.
- Building a business case involves:
- Identifying specific pain points in current QA processes.
- Demonstrating potential ROI through case studies and industry benchmarks.
- Engaging stakeholders by showcasing how AI aligns with broader business goals, such as AI quality assurance and AI in quality assurance.
1.4. Current Challenges in the Quality Assurance Industry
- The QA industry faces several pressing challenges that impact efficiency and product quality:
- Increasing complexity of software systems, making manual testing more difficult.
- Shorter development cycles due to Agile and DevOps practices, leading to time constraints on testing.
- Difficulty in maintaining consistent quality across multiple platforms and devices.
- Resource constraints are common:
- Many QA teams struggle with limited budgets and personnel, impacting their ability to perform thorough testing.
- High turnover rates in QA roles can lead to knowledge gaps and inconsistent testing practices.
- The rise of automation brings its own challenges:
- While automation can improve efficiency, it requires significant upfront investment and expertise.
- There is a risk of over-reliance on automated tests, which may miss critical edge cases.
- Keeping up with evolving technologies and methodologies is essential:
- Continuous learning and adaptation are necessary to stay relevant in a fast-paced industry.
- Many QA professionals report feeling overwhelmed by the rapid pace of change in tools and practices, including AI in QA automation and machine learning for QA.
1.5. The Role of Digital Transformation in Modern QA Practices
- Digital transformation is reshaping how QA teams operate, emphasizing agility and innovation.
- Key aspects of digital transformation in QA include:
- Adoption of cloud-based testing tools, enabling remote collaboration and scalability.
- Integration of AI and machine learning to enhance testing processes and outcomes, such as AI for QA testing and AI for quality control.
- Use of DevOps practices to foster collaboration between development and QA teams.
- Benefits of digital transformation in QA:
- Increased speed and flexibility in testing, allowing for faster feedback loops.
- Enhanced visibility into testing processes through real-time dashboards and analytics.
- Improved customer satisfaction due to higher quality products delivered more quickly.
- Challenges associated with digital transformation:
- Resistance to change from team members accustomed to traditional QA practices.
- The need for ongoing training and upskilling to effectively use new tools and technologies.
- Successful digital transformation requires:
- A clear strategy that aligns QA goals with overall business objectives, including quality assurance for AI.
- Strong leadership support to drive change and foster a culture of innovation.
At Rapid Innovation, we understand these challenges and are equipped to help you navigate them. By leveraging our expertise in AI and blockchain technologies, we can assist you in implementing effective QA solutions that not only enhance your testing processes but also drive significant ROI. Partnering with us means you can expect improved efficiency, reduced costs, and a more agile approach to quality assurance, ultimately leading to greater customer satisfaction and business success.
Refer to the image for a visual representation of the benefits and challenges of integrating AI in Quality Assurance processes.
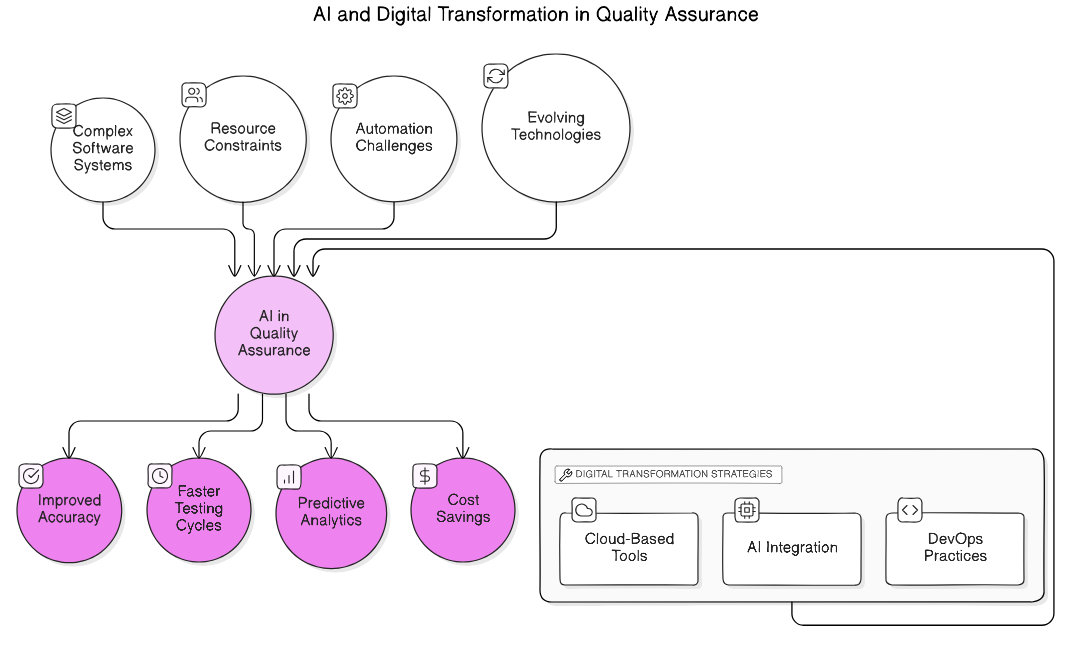
2. Utilizing Computer Vision for Effective Defect Detection
Computer vision is a field of artificial intelligence that enables machines to interpret and make decisions based on visual data. In quality assurance, it plays a crucial role in defect detection, ensuring AI based product management provides specified standards before reaching consumers.
2.1. Fundamentals of Computer Vision in Quality Assurance
- Definition: Computer vision involves the use of algorithms and models to analyze visual data from the world, allowing machines to recognize patterns, objects, and anomalies.
- Importance in Quality Assurance:
- Enhances accuracy in defect detection compared to manual inspection.
- Reduces human error and variability in quality assessments.
- Increases efficiency by processing images at high speeds.
- Key Components:
- Image Acquisition: Capturing images using cameras or sensors.
- Preprocessing: Enhancing image quality through techniques like noise reduction and contrast adjustment.
- Feature Extraction: Identifying relevant features in images, such as edges, shapes, and textures.
- Classification: Using machine learning algorithms to categorize images as defective or non-defective.
- Applications in Various Industries:
- Manufacturing: Inspecting products for surface defects, dimensional accuracy, and assembly errors.
- Food Industry: Ensuring food safety by detecting contaminants or spoilage.
- Electronics: Identifying soldering defects or component misalignments on circuit boards.
- Benefits:
- Consistent quality checks across production lines.
- Real-time monitoring and feedback for immediate corrective actions.
- Cost savings by reducing waste and rework.
2.2. Implementation Approaches for Computer Vision
- Hardware Selection:
- Cameras: Choosing the right type of camera (e.g., CCD, CMOS) based on resolution and speed requirements.
- Lighting: Implementing appropriate lighting conditions to enhance image quality and visibility of defects.
- Software Development:
- Algorithm Design: Developing algorithms for image processing, feature extraction, and classification.
- Machine Learning: Training models using labeled datasets to improve defect detection accuracy.
- Integration: Ensuring the software can communicate with existing production systems for seamless operation.
- System Architecture:
- Edge Computing: Processing images locally on devices to reduce latency and bandwidth usage.
- Cloud Computing: Utilizing cloud resources for heavy computational tasks and data storage.
- Testing and Validation:
- Pilot Programs: Running initial tests on a small scale to evaluate system performance and make adjustments.
- Continuous Learning: Implementing feedback loops to refine algorithms based on new data and defect types.
- Challenges:
- Variability in product appearance: Ensuring the system can adapt to changes in product design or materials.
- Data Quality: Maintaining high-quality labeled datasets for training models.
- Integration with existing workflows: Ensuring that the new system complements current quality assurance processes.
- Future Trends:
- Advancements in deep learning techniques for improved accuracy.
- Increased use of 3D vision systems for more complex defect detection.
- Greater integration of computer vision with IoT devices for real-time monitoring and analytics.
At Rapid Innovation, we leverage our expertise in computer vision for defect detection, including AI based inventory tracking to help clients enhance their quality assurance processes. By implementing tailored computer vision solutions, such as defect detection using computer vision, we enable businesses to achieve greater ROI through improved accuracy, reduced operational costs, and enhanced product quality. Partnering with us means you can expect consistent quality checks, real-time monitoring, and a significant reduction in waste and rework, ultimately driving your business towards greater efficiency and profitability.
Refer to the image for a visual representation of the concepts discussed in "Utilizing Computer Vision for Effective Defect Detection":
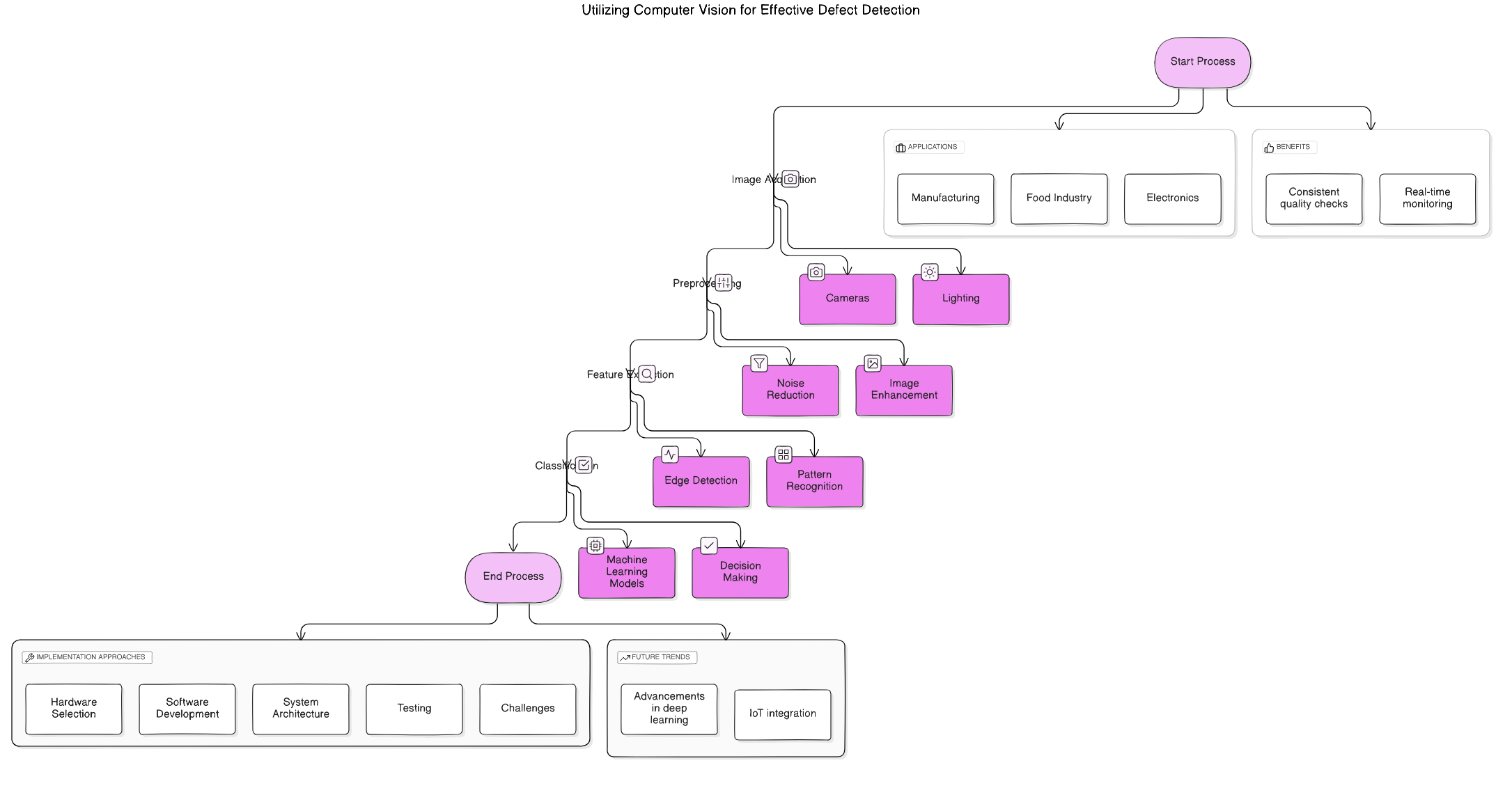
2.3. Key Applications of Computer Vision in Quality Control
Computer vision plays a crucial role in enhancing quality control processes across various industries. Its applications are diverse and impactful, leading to improved efficiency and accuracy.
- Defect Detection: Identifies defects in products during manufacturing and employs sophisticated algorithms to analyze images and detect anomalies, a key aspect of computer vision quality control.
- Measurement and Inspection: Measures dimensions and tolerances of products, ensuring that items meet specified standards and requirements.
- Sorting and Classification: Automatically sorts products based on quality criteria and classifies items into categories for further processing or rejection, which is essential in computer vision for quality control.
- Surface Inspection: Examines surfaces for scratches, dents, or other imperfections, utilizing high-resolution cameras and advanced imaging techniques.
- Assembly Verification: Confirms that components are assembled correctly and utilizes image recognition to ensure proper alignment and placement.
- Real-time Monitoring: Provides continuous monitoring of production lines and enables immediate feedback and corrective actions when issues arise, enhancing the overall quality control computer vision process.
2.4. Advanced Features of Computer Vision Systems
Modern computer vision systems come equipped with advanced features that enhance their functionality and effectiveness in various applications.
- Deep Learning Integration: Utilizes neural networks for improved image recognition and enhances the ability to learn from large datasets and adapt over time.
- 3D Imaging: Captures three-dimensional data for more accurate analysis, useful in applications requiring depth perception and spatial awareness.
- High-Speed Processing: Processes images rapidly to keep up with fast production lines, ensuring minimal delays in quality control checks.
- Multispectral and Hyperspectral Imaging: Analyzes images beyond the visible spectrum and detects materials and defects that are not visible to the naked eye.
- Edge Computing: Performs data processing at the source rather than relying on centralized systems, reducing latency and bandwidth usage, allowing for real-time decision-making.
- User-Friendly Interfaces: Provides intuitive dashboards for operators and simplifies the monitoring and management of quality control processes.
2.5. Integration with Production Lines: Best Practices
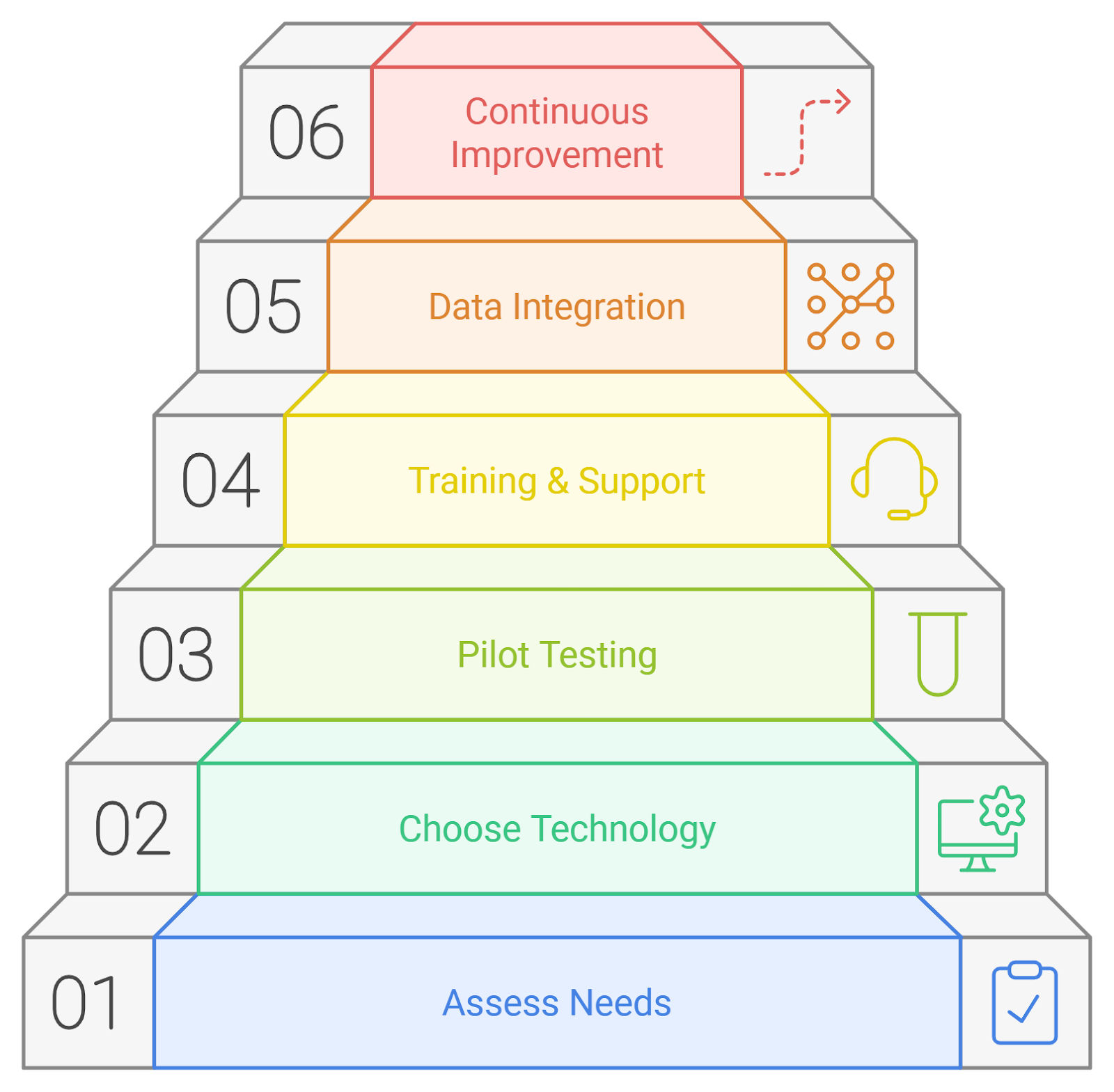
Integrating computer vision systems into production lines requires careful planning and execution to maximize benefits and minimize disruptions.
- Assess Needs and Objectives: Identify specific quality control challenges to address and set clear goals for what the computer vision system should achieve.
- Choose the Right Technology: Select hardware and software that align with production requirements, considering factors such as speed, resolution, and compatibility with existing systems.
- Pilot Testing: Conduct pilot tests to evaluate system performance in real-world conditions and gather feedback from operators to make necessary adjustments.
- Training and Support: Provide comprehensive training for staff on using the system and ensure ongoing technical support for troubleshooting and maintenance.
- Data Integration: Integrate computer vision data with existing production management systems and use data analytics to gain insights and improve decision-making.
- Continuous Improvement: Regularly review system performance and make updates as needed, staying informed about advancements in computer vision technology to enhance capabilities.
3. Implementing Predictive Maintenance Strategies with AI
3.1. Understanding Predictive Maintenance and Its Importance
- Predictive maintenance (PdM) is a proactive approach to maintenance that uses data analysis to predict when equipment will fail or require servicing. It aims to reduce downtime and maintenance costs by addressing issues before they lead to equipment failure.
- Key components of predictive maintenance include:
- Data collection from sensors and equipment.
- Data analysis to identify patterns and trends.
- Predictive algorithms to forecast potential failures.
- Importance of predictive maintenance:
- Cost savings: Reduces unplanned downtime and maintenance costs, leading to significant savings for organizations.
- Increased equipment lifespan: Regular monitoring and timely interventions can extend the life of machinery.
- Enhanced safety: By predicting failures, organizations can prevent accidents and ensure a safer working environment.
- Improved operational efficiency: Streamlined maintenance schedules lead to better resource allocation and productivity.
- Industries benefiting from predictive maintenance include manufacturing, transportation, energy, and healthcare. According to a report by McKinsey, predictive maintenance can reduce maintenance costs by 10-40% and increase equipment uptime by 5-20%. This includes various approaches such as predictive maintenance strategies, preventive predictive and proactive maintenance, and condition based maintenance and predictive maintenance.
3.2. AI Models for Accurate Predictive Maintenance
- AI plays a crucial role in enhancing predictive maintenance strategies by improving the accuracy of predictions and automating data analysis.
- Common AI models used in predictive maintenance include:
- Machine Learning (ML): Algorithms that learn from historical data to identify patterns and predict future failures.
- Deep Learning: A subset of ML that uses neural networks to analyze complex data sets, particularly useful for unstructured data like images and sensor readings.
- Time Series Analysis: Techniques that analyze time-ordered data to forecast future events based on historical trends.
- Benefits of using AI models:
- Enhanced accuracy: AI can process vast amounts of data quickly, leading to more precise predictions.
- Real-time monitoring: AI systems can continuously analyze data from equipment, providing real-time insights and alerts.
- Predictive analytics: AI can identify potential failure points and recommend maintenance actions based on predictive insights, including predictive based maintenance and predictive condition based maintenance.
- Implementation considerations:
- Data quality: High-quality, relevant data is essential for training AI models effectively.
- Integration: AI systems should be integrated with existing maintenance management systems for seamless operation.
- Continuous learning: AI models should be regularly updated with new data to improve their predictive capabilities.
- A study by Deloitte found that organizations using AI for predictive maintenance can achieve a 20% reduction in maintenance costs and a 25% increase in equipment availability. This is particularly relevant for organizations employing predictive and proactive maintenance strategies.
At Rapid Innovation, we specialize in implementing these advanced predictive maintenance strategies tailored to your specific needs. By leveraging our expertise in custom AI model development and blockchain technology, we can help you achieve greater ROI through reduced operational costs, enhanced equipment reliability, and improved safety standards. Partnering with us means you can expect not only innovative solutions but also a commitment to driving efficiency and effectiveness in your operations, including planned maintenance and condition based maintenance. For more information on how AI can enhance predictive maintenance, visit our article on what AI is in predictive maintenance.
3.3. Framework for Implementing Predictive Maintenance
Implementing predictive maintenance (PdM) requires a structured framework to ensure effectiveness and efficiency. The following components are essential:
- Data Collection: Gather data from various sources, including sensors, machinery logs, and maintenance records. Utilize IoT devices for real-time data acquisition.
- Data Analysis: Employ advanced analytics and machine learning algorithms to process the collected data and identify patterns and anomalies that indicate potential failures.
- Predictive Modeling: Develop predictive models based on historical data to forecast equipment failures. Use statistical methods and AI techniques to enhance accuracy.
- Integration with Maintenance Systems: Integrate predictive maintenance insights with existing maintenance management systems (CMMS) to ensure seamless communication between PdM tools and operational workflows.
- Actionable Insights: Generate actionable insights from predictive models to inform maintenance schedules and prioritize maintenance tasks based on risk and impact.
- Continuous Improvement: Regularly review and refine predictive models based on new data and outcomes while fostering a culture of continuous improvement within the maintenance team.
- Training and Change Management: Provide training for staff on new technologies and processes, and manage change effectively to ensure buy-in from all stakeholders.
This framework is part of a broader predictive maintenance framework that emphasizes a data-driven predictive maintenance approach, ensuring that organizations can effectively leverage data to enhance their maintenance strategies.
3.4. Optimizing Maintenance Operations with AI
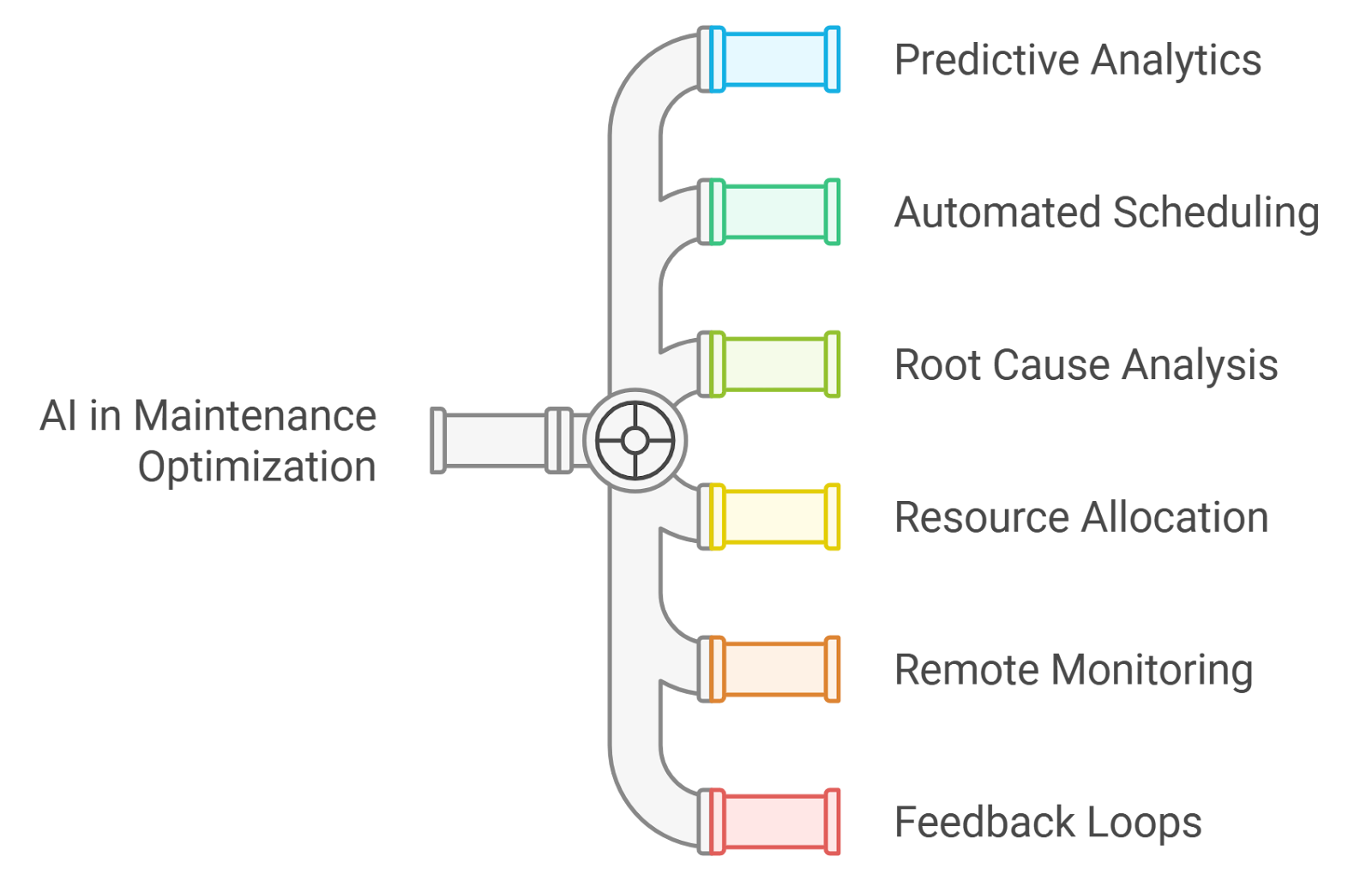
Artificial Intelligence (AI) plays a crucial role in optimizing maintenance operations. Here are key strategies:
- Predictive Analytics: Use AI algorithms to analyze historical data and predict equipment failures before they occur, enhancing decision-making with data-driven insights.
- Automated Scheduling: Implement AI-driven scheduling tools to optimize maintenance tasks based on equipment condition and availability, reducing downtime by aligning maintenance activities with operational needs.
- Root Cause Analysis: Leverage AI to perform root cause analysis of equipment failures, identifying underlying issues that contribute to breakdowns and allowing for targeted interventions.
- Resource Allocation: Optimize resource allocation by using AI to predict the required manpower and materials for maintenance tasks, minimizing waste and improving efficiency.
- Remote Monitoring: Utilize AI for remote monitoring of equipment health, enabling proactive maintenance and reducing the need for on-site inspections while improving response times.
- Feedback Loops: Establish feedback loops where AI systems learn from maintenance outcomes to improve future predictions, continuously refining algorithms based on real-world performance.
3.5. Measuring ROI from Predictive Maintenance
Measuring the return on investment (ROI) from predictive maintenance is essential for justifying expenditures. Key metrics include:
- Cost Savings: Calculate savings from reduced unplanned downtime and emergency repairs, comparing maintenance costs before and after implementing PdM strategies.
- Increased Equipment Lifespan: Assess the impact of predictive maintenance on the lifespan of equipment, as longer equipment life translates to lower capital expenditure over time.
- Improved Productivity: Measure productivity gains from optimized maintenance schedules and reduced downtime, tracking output levels before and after PdM implementation.
- Labor Efficiency: Evaluate changes in labor costs and efficiency due to better resource allocation and scheduling, analyzing the time saved on maintenance tasks.
- Customer Satisfaction: Monitor customer satisfaction levels as a result of improved service reliability, as higher satisfaction can lead to increased sales and customer loyalty.
- Data-Driven Decision Making: Assess the value of insights gained from predictive analytics in making informed decisions, as improved decision-making can lead to better strategic planning and resource management.
- Benchmarking: Compare ROI metrics against industry standards or similar organizations, using benchmarking to identify areas for improvement and validate PdM effectiveness.
By partnering with Rapid Innovation, clients can leverage our expertise in AI and blockchain technologies to implement these frameworks effectively. Our tailored solutions not only enhance operational efficiency but also drive significant ROI through reduced costs, improved productivity, and increased customer satisfaction. With our commitment to continuous improvement and innovation, we empower organizations to stay ahead in a competitive landscape.
4. Root Cause Analysis (RCA) Using AI for Continuous Improvement
Root Cause Analysis (RCA) is a systematic approach to identifying the underlying causes of problems or incidents. By utilizing Artificial Intelligence (AI), organizations can enhance their RCA processes, leading to more effective solutions and continuous improvement.
4.1. AI-Powered RCA Framework: An Overview
An AI-powered RCA framework integrates advanced technologies to streamline the identification and analysis of root causes. This framework typically includes the following components:
- Data Collection: AI systems can gather data from various sources, including operational logs, incident reports, and sensor data. Automated data collection reduces human error and ensures comprehensive data coverage.
- Data Analysis: Machine learning algorithms analyze large datasets to identify patterns and correlations that may not be immediately apparent. AI can process data faster than traditional methods, allowing for quicker insights.
- Visualization Tools: AI frameworks often include visualization tools that present data in an easily digestible format. These tools help stakeholders understand complex data relationships and trends.
- Predictive Analytics: AI can predict potential issues before they occur by analyzing historical data and identifying risk factors. This proactive approach allows organizations to address problems before they escalate.
- Continuous Learning: AI systems can learn from past incidents and improve their analysis over time. This continuous learning aspect ensures that the RCA process evolves and adapts to new challenges.
4.2. Leveraging Machine Learning Techniques for RCA
Machine learning (ML) techniques play a crucial role in enhancing the effectiveness of RCA. Here are some key ways ML can be leveraged:
- Anomaly Detection: ML algorithms can identify anomalies in data that may indicate underlying issues. By flagging unusual patterns, organizations can investigate potential root causes more efficiently. For more information on anomaly detection, visit this link.
- Classification and Clustering: ML can classify incidents based on historical data, helping to categorize problems and identify common root causes. Clustering techniques group similar incidents, making it easier to analyze trends and recurring issues.
- Natural Language Processing (NLP): NLP can analyze unstructured data, such as incident reports and customer feedback, to extract relevant information. This capability allows organizations to gain insights from qualitative data that may otherwise be overlooked, including insights from 'ai root cause analysis' and 'root cause analysis ai'.
- Decision Trees and Random Forests: These ML models can help identify the most significant factors contributing to a problem. By evaluating various variables, organizations can prioritize their focus on the most impactful root causes.
- Feedback Loops: Implementing feedback loops in ML models allows for continuous refinement of the RCA process. As new data becomes available, models can be updated to improve accuracy and relevance.
By integrating AI and machine learning into the RCA process, organizations can achieve a more thorough understanding of issues, leading to effective solutions and ongoing improvements. Partnering with Rapid Innovation enables clients to leverage these advanced technologies, ensuring a more efficient and effective approach to problem-solving that ultimately drives greater ROI. Our expertise in AI and blockchain development empowers organizations to not only identify root causes but also implement sustainable solutions that foster continuous improvement and operational excellence.
4.3. Strategies for Implementing RCA with AI
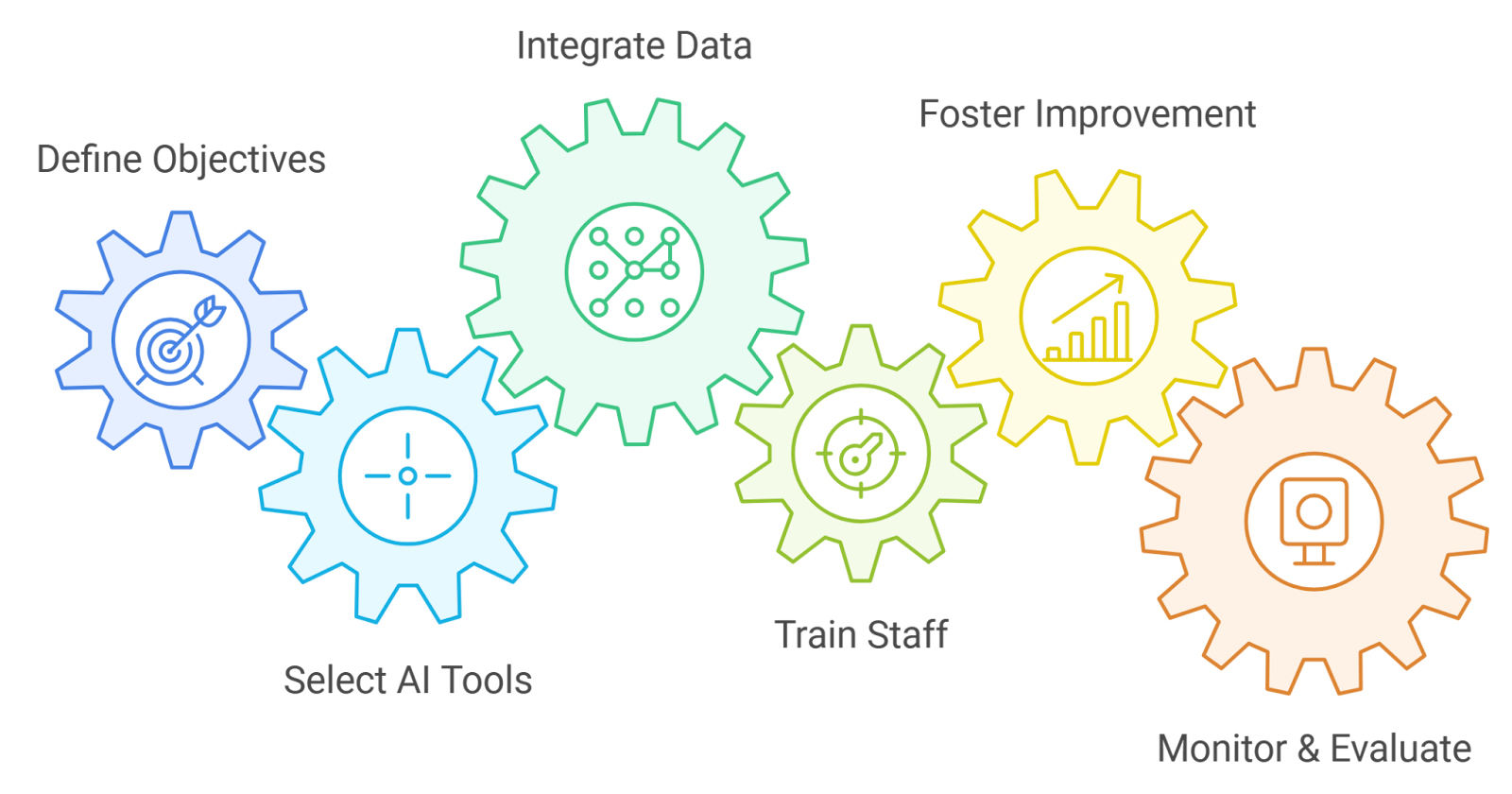
- Define clear objectives: Establish what you aim to achieve with Root Cause Analysis (RCA) using AI. This could include reducing errors, improving patient safety, or enhancing operational efficiency.
- Select appropriate AI tools: Choose AI technologies that align with your RCA goals. Options may include machine learning algorithms, natural language processing, or predictive analytics.
- Integrate data sources: Ensure that AI systems can access and analyze data from various sources, such as electronic health records, incident reports, and patient feedback. This comprehensive data integration is crucial for effective RCA.
- Train staff: Provide training for staff on how to use AI tools effectively. This includes understanding AI outputs and how to interpret data for RCA.
- Foster a culture of continuous improvement: Encourage a mindset that values learning from mistakes. This cultural shift can enhance the effectiveness of RCA initiatives.
- Monitor and evaluate: Regularly assess the effectiveness of AI-driven RCA processes. Use metrics to measure improvements and identify areas for further enhancement.
4.4. Advanced Analytics for Comprehensive RCA
- Utilize predictive analytics: Leverage predictive models to identify potential issues before they occur. This proactive approach can help in addressing root causes before they escalate.
- Implement data visualization tools: Use advanced visualization techniques to present RCA findings clearly. This can help stakeholders understand complex data and trends.
- Analyze unstructured data: Incorporate unstructured data sources, such as social media feedback or open-ended survey responses, into your RCA process. Advanced analytics can extract valuable insights from this data.
- Employ machine learning algorithms: Use machine learning to identify patterns and correlations in large datasets. This can uncover hidden root causes that traditional analysis might miss.
- Conduct scenario analysis: Use advanced analytics to simulate different scenarios and their potential impacts. This can help in understanding the implications of various root causes.
- Collaborate with data scientists: Work with data analytics professionals to enhance your RCA capabilities. Their expertise can help in developing more sophisticated analytical models.
4.5. Action Planning for Quality Improvement
- Set specific goals: Define clear, measurable objectives for quality improvement initiatives based on RCA findings. This ensures that actions are targeted and effective.
- Develop an action plan: Create a detailed plan outlining the steps needed to address identified root causes. Include timelines, responsible parties, and required resources.
- Engage stakeholders: Involve relevant stakeholders in the action planning process. This can include staff, management, and patients, ensuring that diverse perspectives are considered.
- Monitor progress: Establish metrics to track the implementation of action plans. Regularly review progress to ensure that quality improvement efforts are on track.
- Adjust as necessary: Be prepared to modify action plans based on feedback and results. Flexibility is key to responding to unforeseen challenges.
- Communicate outcomes: Share the results of quality improvement initiatives with all stakeholders. Transparency fosters trust and encourages ongoing participation in RCA efforts.
At Rapid Innovation, we understand that implementing these strategies effectively can lead to significant improvements in operational efficiency and overall quality. By partnering with us, clients can expect tailored solutions that not only enhance their ai root cause analysis processes but also drive greater ROI through reduced errors and improved decision-making capabilities. Our expertise in root cause analysis ai and advanced analytics ensures that your organization can leverage data-driven insights to foster a culture of continuous improvement, ultimately leading to better outcomes and increased stakeholder satisfaction.
5. Integrating Smart Sensors and IoT for Enhanced Quality Control
The integration of smart sensors and the Internet of Things (IoT) in quality control processes is revolutionizing how industries monitor and maintain product quality. By leveraging real-time data and advanced analytics, organizations can enhance their quality assurance practices, leading to improved efficiency and reduced waste.
5.1. Understanding IoT Architecture in Quality Assurance
IoT architecture in quality assurance consists of several key components that work together to facilitate data collection, analysis, and decision-making.
- Devices and Sensors: Smart sensors collect data from the production environment, such as temperature, humidity, and pressure. These smart sensors can be embedded in machinery or products to monitor conditions continuously.
- Connectivity: Data from sensors is transmitted via various communication protocols (e.g., Wi-Fi, Bluetooth, Zigbee) to a central system. Reliable connectivity ensures that data is transmitted in real-time for immediate analysis.
- Data Processing: Collected data is processed using edge computing or cloud computing solutions. Edge computing allows for real-time processing at the source, reducing latency and bandwidth usage.
- Analytics and Insights: Advanced analytics tools, including machine learning algorithms, analyze the data to identify patterns and anomalies. Insights derived from data help in making informed decisions regarding quality control measures.
- User Interface: Dashboards and visualization tools present data in an easily digestible format for quality assurance teams. User-friendly interfaces enable quick access to critical information for timely interventions.
- Feedback Loop: Continuous monitoring creates a feedback loop that allows for ongoing adjustments to processes. This iterative approach helps in maintaining high-quality standards and reducing defects.
5.2. Strategies for Effective Sensor Implementation
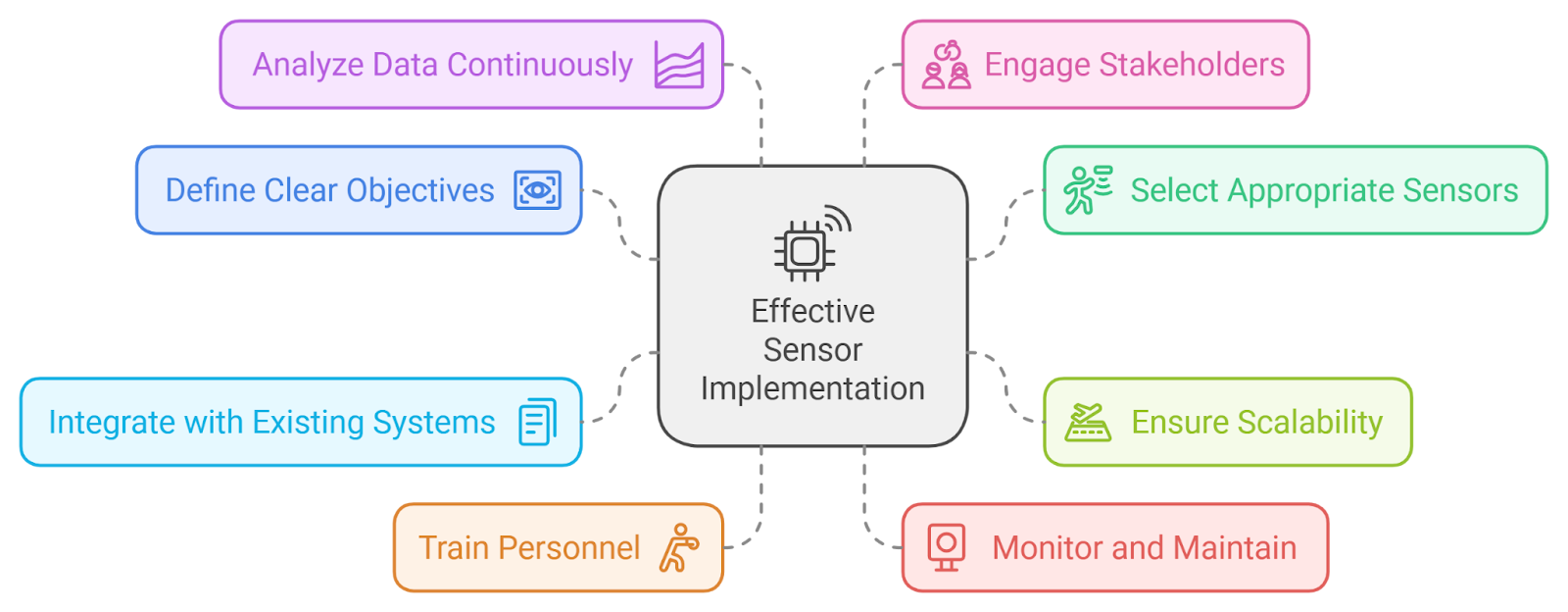
Implementing smart sensors effectively requires careful planning and execution. Here are some strategies to consider:
- Define Clear Objectives: Establish specific quality control goals that the smart sensors implementation aims to achieve. Objectives may include reducing defect rates, improving compliance, or enhancing product consistency.
- Select Appropriate Sensors: Choose sensors that are suitable for the specific environment and conditions of the production process. Consider factors such as accuracy, range, durability, and compatibility with existing systems.
- Ensure Scalability: Design the sensor network to be scalable, allowing for future expansion as needs evolve. A modular approach enables the addition of new smart sensors without overhauling the entire system.
- Integrate with Existing Systems: Ensure that the new sensors can seamlessly integrate with existing quality management systems (QMS). Compatibility with software platforms is crucial for effective data sharing and analysis.
- Train Personnel: Provide training for staff on how to use and maintain the smart sensors effectively. Empowering employees with knowledge ensures that they can leverage the technology to its fullest potential.
- Monitor and Maintain: Regularly check the performance of sensors to ensure they are functioning correctly. Implement a maintenance schedule to address any issues promptly and avoid data inaccuracies.
- Analyze Data Continuously: Establish a routine for analyzing data collected from smart sensors to identify trends and areas for improvement. Continuous analysis helps in making proactive adjustments to quality control processes.
- Engage Stakeholders: Involve all relevant stakeholders, including production teams, quality assurance personnel, and IT staff, in the implementation process. Collaboration ensures that the system meets the needs of all parties involved.
By integrating smart sensors and IoT into quality control processes, organizations can achieve significant improvements in product quality, operational efficiency, and customer satisfaction. Partnering with Rapid Innovation allows you to harness these advanced technologies effectively, ensuring a greater return on investment and a competitive edge in your industry. Our expertise in AI and blockchain development will guide you through the AI process optimization, maximizing the benefits of your quality control initiatives.
5.3. Managing Data from IoT Devices
Managing data from IoT devices is crucial for organizations to derive meaningful insights and improve operational efficiency. The vast amount of data generated by these devices can be overwhelming, but with the right strategies, it can be effectively managed.
- Data Collection: Utilize cloud platforms for scalable data storage and implement edge computing to process data closer to the source, reducing latency. This approach not only enhances speed but also optimizes resource utilization, leading to cost savings. An effective iot data management platform can streamline this process.
- Data Processing: Use real-time data processing frameworks to analyze data as it comes in and employ batch processing for historical data analysis to identify trends. This dual approach allows organizations to make informed decisions quickly while also understanding long-term patterns. Understanding data management in iot is essential for this step.
- Data Security: Implement encryption protocols to protect data in transit and at rest, and regularly update firmware on IoT devices to mitigate vulnerabilities. By prioritizing security, organizations can safeguard their data assets and maintain customer trust. This is particularly important in industrial iot data management.
- Data Integration: Use APIs to integrate data from various IoT devices into a centralized system and employ data lakes to store unstructured data for future analysis. This integration fosters a holistic view of operations, enabling better strategic planning. A robust internet of things data management strategy can enhance this integration.
- Data Visualization: Utilize dashboards to present data in an easily digestible format and implement machine learning algorithms to predict outcomes based on historical data. Effective visualization empowers stakeholders to make data-driven decisions swiftly. Tools like grafana aws iot can be beneficial for this purpose. For organizations looking to enhance their machine learning capabilities, our MLOps consulting services can provide the necessary expertise and support.
5.4. Advanced Applications of IoT in Quality Assurance
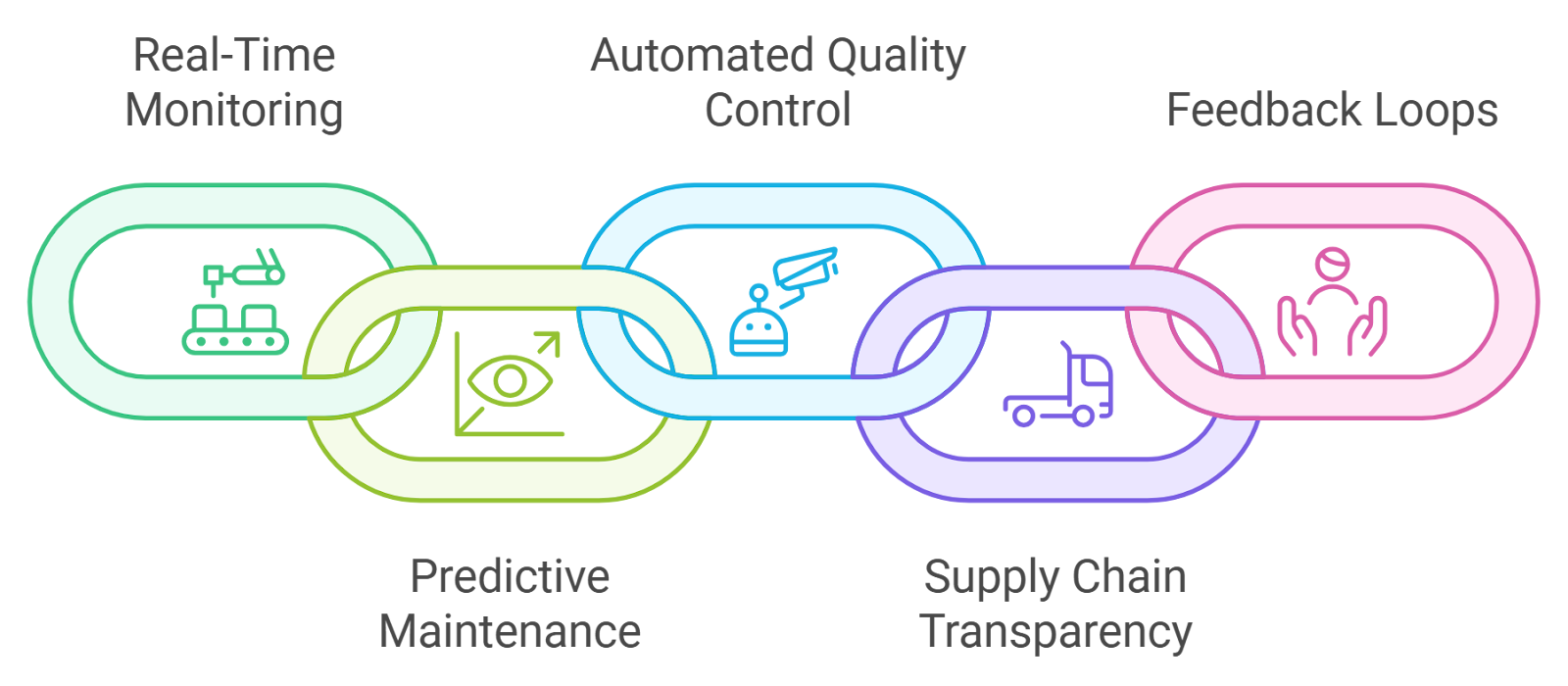
The integration of IoT in quality assurance (QA) processes has opened up new avenues for enhancing product quality and operational efficiency. Advanced applications of IoT in QA include:
- Real-Time Monitoring: Continuous monitoring of production processes ensures compliance with quality standards. The use of sensors to detect anomalies in real-time allows for immediate corrective actions, minimizing defects and enhancing product reliability.
- Predictive Maintenance: Analyzing data from IoT devices can predict equipment failures before they occur. Scheduling maintenance activities based on actual usage and performance data helps reduce downtime, ultimately leading to increased productivity and cost efficiency.
- Automated Quality Control: Implementing automated inspection systems using IoT-enabled cameras and sensors enhances quality control. Machine learning algorithms can be used to improve defect detection rates, ensuring that only the highest quality products reach the market.
- Supply Chain Transparency: Tracking products throughout the supply chain using IoT devices ensures quality at every stage. Monitoring environmental conditions (temperature, humidity) during transportation helps maintain product integrity, reducing waste and enhancing customer satisfaction.
- Feedback Loops: Collecting data from end-users identifies quality issues and areas for improvement. IoT data can inform product design and development processes, leading to innovations that better meet customer needs.
5.5. System Integration Strategies for IoT and QA
Integrating IoT systems with quality assurance processes requires a strategic approach to ensure seamless operation and data flow. Effective integration strategies include:
- Unified Data Architecture: Develop a centralized data architecture that allows for easy access and sharing of data across systems. Use data standards and protocols to ensure compatibility between IoT devices and QA systems, facilitating smoother operations.
- Interoperability: Choose IoT devices and platforms that support open standards to facilitate integration. Implement middleware solutions to bridge gaps between different systems and devices, ensuring a cohesive operational environment.
- Collaboration Tools: Utilize collaboration platforms that allow teams to share insights and data in real-time. Foster communication between IT, QA, and operations teams to align goals and processes, enhancing overall efficiency.
- Scalability: Design systems that can easily scale as the number of IoT devices increases. Use cloud-based solutions to accommodate growing data storage and processing needs, ensuring that your infrastructure can support future growth.
- Continuous Improvement: Regularly review and update integration strategies based on feedback and performance metrics. Implement agile methodologies to adapt quickly to changes in technology and business requirements, ensuring that your organization remains competitive and responsive to market demands.
By partnering with Rapid Innovation, organizations can leverage our expertise in AI and Blockchain to implement these strategies effectively. Our tailored solutions not only enhance operational efficiency but also drive greater ROI, enabling clients to achieve their business goals with confidence.
6. Creating an Integrated Quality Management System (IQMS)
An Integrated Quality Management System (IQMS) is essential for organizations aiming to enhance their quality processes and ensure compliance with industry standards. An IQMS integrates various quality management processes, such as integrated quality management, integrated quality assurance, and integrated quality control, into a cohesive framework, allowing for better data management, improved decision-making, and streamlined operations.
6.1. Designing the System Architecture
Designing the architecture of an IQMS involves several critical steps to ensure that it meets the organization's needs effectively.
- Define Objectives and Scope
Identify the specific quality goals of the organization and determine the scope of the IQMS, including which processes and departments will be included. - Select Appropriate Framework
Choose a quality management framework (e.g., ISO 9001, Six Sigma) that aligns with organizational goals and ensure the framework supports integration with existing systems. - Establish Data Flow
Map out how data will flow through the system, including inputs, processes, and outputs. Identify key data sources and ensure they are integrated into the IQMS. - User Roles and Permissions
Define user roles and access levels to ensure data security and integrity. Create a hierarchy of permissions based on job functions. - Technology Selection
Choose the right technology stack, including software and hardware, to support the IQMS. Consider cloud-based solutions for scalability and accessibility, such as enterprise wide quality integrated management software. - System Integration
Ensure the IQMS can integrate with other enterprise systems (e.g., ERP, CRM) and use APIs and middleware to facilitate seamless data exchange. - User Interface Design
Design an intuitive user interface that enhances user experience and ensure that the system is user-friendly to encourage adoption.
6.2. Implementing Real-time Monitoring Capabilities
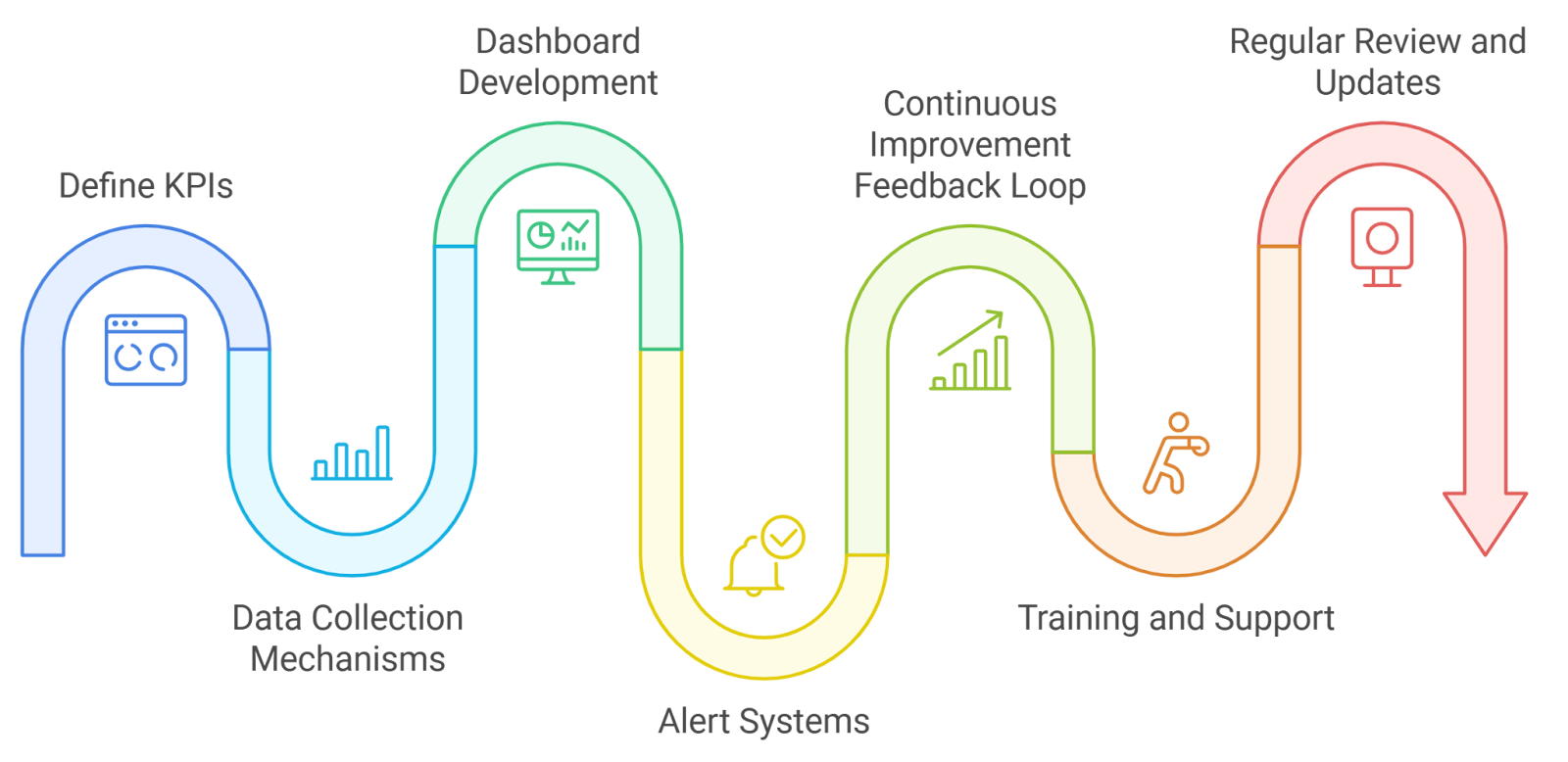
Real-time monitoring is a crucial component of an IQMS, enabling organizations to track quality metrics and respond to issues promptly.
- Define Key Performance Indicators (KPIs)
Identify the KPIs that will be monitored in real-time and ensure KPIs align with organizational quality objectives. - Data Collection Mechanisms
Implement automated data collection tools to gather information from various sources and use sensors and IoT devices for real-time data acquisition in manufacturing processes. - Dashboard Development
Create dashboards that display real-time data in an easily digestible format, including visualizations such as graphs and charts to highlight trends and anomalies. - Alert Systems
Set up alert mechanisms to notify relevant personnel of deviations from quality standards. Use email, SMS, or in-app notifications for immediate communication. - Continuous Improvement Feedback Loop
Establish a feedback loop that allows for continuous monitoring and improvement. Use real-time data to inform decision-making and drive process enhancements. - Training and Support
Provide training for staff on how to use real-time monitoring tools effectively and ensure ongoing support is available to address any technical issues. - Regular Review and Updates
Schedule regular reviews of the monitoring system to ensure it remains effective and update KPIs and monitoring tools as organizational needs evolve.
By partnering with Rapid Innovation, organizations can leverage our expertise in developing and implementing an Integrated Quality Management System tailored to their specific needs, including integrated quality management system for Wipro and integrated quality management system in education. Our approach not only enhances operational efficiency but also drives greater ROI through improved quality control and compliance. Clients can expect benefits such as reduced operational costs, increased customer satisfaction, and a more agile response to market changes, ultimately leading to sustained business growth. Additionally, understanding the critical role of data quality in AI implementations is vital for ensuring the effectiveness of the IQMS.
6.3. Building a Decision Support System
A Decision Support System (DSS) is a computer-based information system that supports business or organizational decision-making activities. Building an effective clinical decision support system involves several key components and steps:
- Define Objectives: Clearly outline the goals of the DSS. What decisions will it support?
- Data Collection: Gather relevant data from various sources. This can include:
- Internal databases
- External data sources
- Real-time data feeds
- Data Processing: Organize and process the collected data to ensure it is usable. This may involve:
- Data cleaning
- Data integration
- Data transformation
- Model Development: Create models that will help in decision-making. This can include:
- Statistical models
- Predictive analytics
- Simulation models
- User Interface Design: Develop an intuitive interface that allows users to interact with the DSS easily. Consider:
- Visualizations
- Dashboards
- Reporting tools
- Testing and Validation: Ensure the system works as intended. This involves:
- User testing
- Performance evaluation
- Validation against real-world scenarios
- Implementation and Training: Roll out the DSS and provide training for users to maximize its effectiveness.
- Feedback and Iteration: Continuously gather user feedback and make necessary adjustments to improve the system.
A well-constructed clinical support system can significantly enhance decision-making efficiency and effectiveness, leading to better outcomes for organizations. For a detailed guide on AI development for businesses, you can refer to this resource.
7. Comprehensive Implementation Guide for AI in Quality Assurance
Implementing AI in quality assurance (QA) can transform how organizations ensure product quality. A comprehensive guide for this implementation includes several critical steps:
- Assess Current QA Processes: Evaluate existing QA practices to identify areas for improvement. Consider:
- Manual testing processes
- Automation levels
- Common defects and issues
- Define AI Objectives: Establish clear goals for AI integration. This may include:
- Reducing testing time
- Increasing defect detection rates
- Enhancing test coverage
- Select Appropriate AI Tools: Choose AI tools that align with your objectives. Options may include:
- Machine learning algorithms
- Natural language processing
- Computer vision for visual inspections
- Data Preparation: Prepare data for AI training. This involves:
- Collecting historical QA data
- Labeling data for supervised learning
- Ensuring data quality and relevance
- Pilot Testing: Implement a pilot project to test AI tools in a controlled environment. This helps to:
- Validate AI effectiveness
- Identify potential challenges
- Gather user feedback
- Integration with Existing Systems: Ensure that AI tools can seamlessly integrate with current QA processes and tools. This may require:
- API development
- Workflow adjustments
- Training and Change Management: Provide training for QA teams on new AI tools and processes. Focus on:
- Upskilling employees
- Managing resistance to change
- Monitor and Evaluate: Continuously monitor AI performance and evaluate its impact on QA processes. Key metrics to track include:
- Defect rates
- Testing efficiency
- User satisfaction
- Iterate and Improve: Use feedback and performance data to refine AI tools and processes over time.
By following this guide, organizations can effectively implement AI in their quality assurance processes, leading to improved product quality and operational efficiency.
7.1. Project Planning for Successful Implementation
Effective project planning is crucial for the successful implementation of AI in quality assurance. Key elements of project planning include:
- Establish a Project Team: Form a dedicated team with diverse skills, including:
- QA specialists
- Data scientists
- Project managers
- Define Scope and Objectives: Clearly outline the project scope and specific objectives. This should include:
- What AI technologies will be used
- Expected outcomes and benefits
- Develop a Timeline: Create a realistic timeline for the project, including:
- Key milestones
- Deadlines for each phase
- Budgeting: Estimate the budget required for the project, considering:
- Tool and technology costs
- Training expenses
- Resource allocation
- Risk Assessment: Identify potential risks and develop mitigation strategies. Common risks may include:
- Resistance to change
- Data quality issues
- Integration challenges
- Stakeholder Engagement: Involve key stakeholders throughout the project. This includes:
- Regular updates
- Feedback sessions
- Addressing concerns
- Documentation: Maintain thorough documentation of all project phases, including:
- Requirements
- Design decisions
- Testing results
- Review and Adjust: Regularly review project progress and make adjustments as necessary to stay on track.
By focusing on these elements, organizations can enhance their chances of successfully implementing AI in quality assurance, leading to improved processes and outcomes.
At Rapid Innovation, we understand the complexities of integrating advanced technologies like AI and blockchain into your business processes. Our expertise in building tailored clinical decision support systems and implementing AI in quality assurance can help you achieve greater ROI by streamlining operations, enhancing decision-making, and improving product quality.
When you partner with us, you can expect:
- Increased Efficiency: Our solutions are designed to optimize your workflows, reducing time and resources spent on manual processes.
- Enhanced Decision-Making: With our decision support system, you will have access to real-time data and predictive analytics, empowering you to make informed decisions quickly.
- Improved Quality Assurance: Our AI-driven QA processes will help you detect defects earlier, ensuring higher product quality and customer satisfaction.
- Ongoing Support and Training: We provide comprehensive training and support to ensure your team is equipped to leverage new technologies effectively.
Let us help you navigate the future of technology and achieve your business goals efficiently and effectively.
7.2. Deployment Strategies for AI Solutions
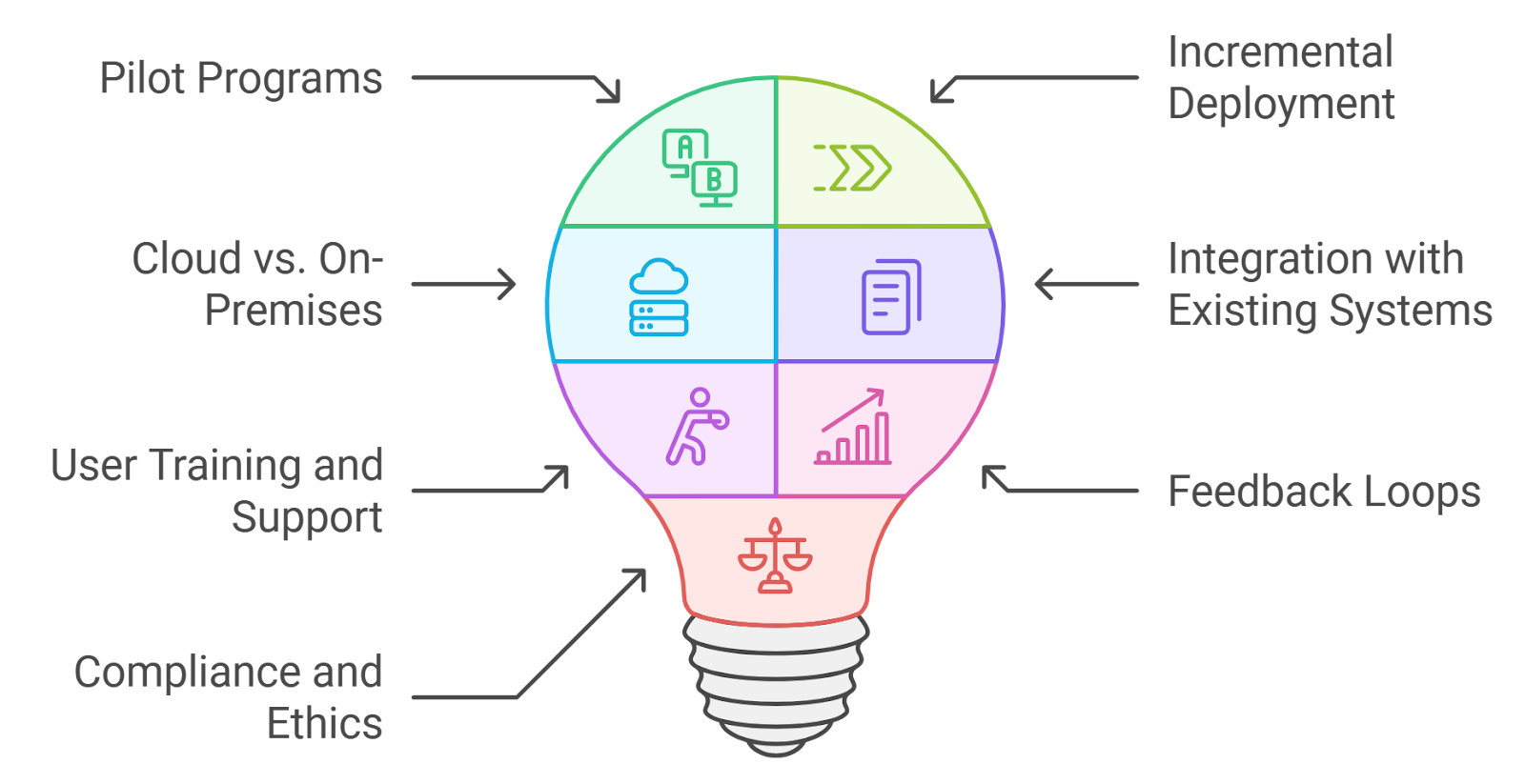
Deploying AI solutions requires careful planning and execution to ensure they meet business objectives and integrate seamlessly into existing systems. Here are some effective strategies:
- Pilot Programs: Start with a small-scale pilot to test the AI solution in a controlled environment. This allows for adjustments based on real-world feedback before a full rollout.
- Incremental Deployment: Gradually introduce the AI solution across different departments or functions. This helps in managing risks and allows teams to adapt to the new technology.
- Cloud vs. On-Premises: Decide whether to deploy the AI solution in the cloud or on-premises. Cloud solutions offer scalability and flexibility, while on-premises solutions may provide more control over data security.
- Integration with Existing Systems: Ensure that the AI solution can integrate with current software and workflows. This minimizes disruption and enhances user adoption.
- User Training and Support: Provide comprehensive training for users to familiarize them with the AI tools. Ongoing support is crucial for addressing any issues that arise post-deployment.
- Feedback Loops: Establish mechanisms for collecting user feedback and performance data. This information is vital for continuous improvement of the AI solution.
- Compliance and Ethics: Ensure that the deployment adheres to legal and ethical standards, particularly regarding data privacy and security.
7.3. Measuring Success through Metrics
Measuring the success of AI implementations is essential for understanding their impact and guiding future improvements. Key metrics to consider include:
- Accuracy and Performance: Evaluate how accurately the AI solution performs its intended tasks. Metrics like precision, recall, and F1 score are commonly used in machine learning contexts.
- Return on Investment (ROI): Calculate the financial benefits gained from the AI solution compared to its costs. This can include savings from increased efficiency or reduced error rates.
- User Adoption Rates: Monitor how many users are actively engaging with the AI solution. High adoption rates often indicate that the solution is user-friendly and meets user needs.
- Time Savings: Measure the reduction in time taken to complete tasks before and after AI implementation. This can highlight efficiency gains.
- Customer Satisfaction: For customer-facing AI solutions, track customer feedback and satisfaction scores to assess the impact on user experience.
- Error Reduction: Analyze the decrease in errors or defects in processes where AI has been implemented. This is particularly relevant in quality assurance contexts.
- Scalability: Assess how well the AI solution scales with increased data or user load. A successful AI deployment should maintain performance as demands grow.
7.4. Case Studies: Successful Implementations of AI in QA
Several organizations have successfully implemented AI in their quality assurance processes, leading to significant improvements. Here are a few notable case studies:
- Facebook: Facebook uses AI to enhance its content moderation processes. By employing machine learning algorithms, the platform can automatically detect and remove harmful content, significantly reducing the time taken for manual reviews.
- Tesla: Tesla integrates AI in its vehicle testing and quality assurance processes. The company uses AI-driven analytics to monitor vehicle performance and identify potential issues before they reach customers, improving overall product quality.
- IBM: IBM's Watson has been utilized in various QA applications, particularly in software testing. By automating test case generation and execution, IBM has reduced testing time and improved accuracy, allowing teams to focus on more complex tasks.
- Microsoft: Microsoft employs AI in its Azure DevOps services to enhance software quality. The AI analyzes code changes and predicts potential bugs, enabling developers to address issues proactively.
- Siemens: Siemens has implemented AI in its manufacturing quality assurance processes. By using AI to analyze production data, the company can identify defects early in the manufacturing process, leading to higher quality products and reduced waste.
By partnering with Rapid Innovation, clients can leverage these ai deployment strategies and success metrics to ensure their AI solutions are not only effective but also aligned with their business goals, ultimately driving greater ROI and operational efficiency.
7.5. Future Trends in AI for Quality Assurance
- Increased Automation: AI will continue to automate repetitive tasks in quality assurance, reducing human error and increasing efficiency. Tools like automated testing frameworks will become more sophisticated, allowing for seamless integration with development processes. This includes the use of ai for qa and ai for qa testing to streamline workflows.
- Enhanced Predictive Analytics: AI will leverage big data to predict potential quality issues before they arise. Predictive models will analyze historical data to identify patterns and trends, enabling proactive measures. This approach aligns with ai quality assurance practices that focus on anticipating challenges.
- Integration of Machine Learning: Machine learning algorithms will improve the accuracy of quality assessments by learning from past data. Continuous learning will allow AI systems to adapt to new challenges and improve over time, particularly in areas like machine learning for qa.
- Natural Language Processing (NLP): NLP will facilitate better communication between teams by analyzing feedback and documentation. AI-driven chatbots will assist in resolving quality-related queries in real-time, enhancing the overall ai in quality assurance experience.
- Shift Towards DevOps and Continuous Testing: AI will play a crucial role in the DevOps culture, promoting continuous testing and integration. This shift will ensure that quality assurance is an ongoing process rather than a final step, reinforcing the importance of qa for ai initiatives.
- Enhanced User Experience Testing: AI will enable more comprehensive user experience testing by simulating real user interactions. This will help identify usability issues that may not be apparent through traditional testing methods, particularly in the context of ai in software quality assurance.
- Focus on Security Testing: As cyber threats increase, AI will be used to enhance security testing processes. AI tools will identify vulnerabilities and ensure compliance with security standards, which is critical for quality assurance for ai applications.
- Greater Collaboration Between AI and Human Testers: The future will see a hybrid approach where AI tools assist human testers rather than replace them. This collaboration will combine the strengths of both AI and human intuition for better quality outcomes, especially in ai in qa automation.
8. Conclusion
- The integration of AI in quality assurance is transforming the landscape of software development. AI technologies are enhancing efficiency, accuracy, and speed in testing processes. Organizations that adopt AI-driven quality assurance practices are likely to gain a competitive edge.
8.1. Summarizing Key Insights from AI in Quality Assurance
AI is revolutionizing quality assurance by automating repetitive tasks and reducing human error. Predictive analytics powered by AI can foresee potential quality issues, allowing for proactive solutions. Machine learning enhances the accuracy of quality assessments by continuously learning from data. Natural Language Processing improves communication and feedback analysis within teams. The shift towards DevOps and continuous testing emphasizes the importance of ongoing quality assurance. AI-driven user experience testing provides deeper insights into usability issues. Security testing is becoming increasingly important, with AI tools identifying vulnerabilities. The future of quality assurance will involve collaboration between AI technologies and human testers, leveraging the strengths of both.
At Rapid Innovation, we understand the importance of these trends and are committed to helping our clients navigate the evolving landscape of AI in quality assurance. By partnering with us, you can expect enhanced efficiency, reduced costs, and improved quality outcomes, ultimately leading to greater ROI for your organization. Our expertise in AI and blockchain development ensures that you are equipped with the latest tools and strategies to stay ahead of the competition. Let us help you achieve your goals effectively and efficiently. For more information on our services, check out our adaptive AI development and learn more about elevating manufacturing quality control with AI-enhanced RPA..
8.2. The Future of Quality Assurance in the Age of AI
- AI is transforming quality assurance (QA) by automating repetitive tasks and enhancing decision-making processes, allowing teams to focus on more strategic initiatives such as ai for qa and ai quality assurance.
- Predictive analytics powered by AI can identify potential defects before they occur, leading to proactive quality management and reducing costly post-release fixes, particularly in artificial intelligence assurance.
- Machine learning algorithms can analyze vast amounts of data to uncover patterns and insights that human testers might miss, ultimately improving the accuracy of testing outcomes in ai in quality assurance.
- Continuous testing and integration are becoming more feasible with AI, allowing for faster release cycles without compromising quality, which can significantly enhance your competitive edge, especially in ai for qa testing.
- AI-driven tools can facilitate real-time feedback, enabling teams to address issues immediately rather than waiting for post-release evaluations, thus minimizing downtime and maximizing productivity in ai in software quality assurance.
- The role of QA professionals is evolving; they will need to focus more on strategic oversight and less on manual testing, allowing for a more efficient allocation of resources, particularly in qa for ai.
- Ethical considerations are crucial, as AI systems must be designed to avoid biases and ensure fairness in testing processes, fostering trust and integrity in your products, which is essential for quality assurance for ai. For more insights on successful AI integration strategies, visit this link.
8.3. Recommendations for Businesses Implementing AI in QA
- Start with a clear strategy: Define the goals and objectives for integrating AI into your QA processes to ensure alignment with your overall business strategy, including ai in qa automation.
- Invest in training: Equip your QA team with the necessary skills to work alongside AI tools effectively, enhancing their capabilities and boosting team morale.
- Choose the right tools: Select AI-driven QA tools that align with your business needs and can integrate seamlessly with existing systems, ensuring a smooth transition and maximizing ROI.
- Focus on data quality: Ensure that the data used for training AI models is accurate, relevant, and representative of real-world scenarios to improve the reliability of your testing processes.
- Implement gradual changes: Begin with pilot projects to test AI applications in QA before scaling up to full implementation, allowing for adjustments based on initial findings.
- Foster collaboration: Encourage communication between QA teams, developers, and data scientists to ensure a cohesive approach to quality assurance, leading to better outcomes.
- Monitor and evaluate: Continuously assess the performance of AI tools and their impact on QA processes, making adjustments as necessary to optimize efficiency and effectiveness.
8.4. Final Thoughts: Embracing Innovation for Quality Excellence
- The integration of AI in QA represents a significant shift towards more efficient and effective quality management, positioning your organization for future success.
- Businesses that embrace AI technologies can achieve higher levels of quality, faster time-to-market, and improved customer satisfaction, ultimately driving greater ROI.
- Innovation in QA is not just about adopting new tools; it requires a cultural shift towards continuous improvement and adaptability, fostering a mindset of excellence.
- Companies should remain vigilant about the ethical implications of AI, ensuring that their practices promote fairness and transparency, which is essential for maintaining customer trust.
- As the landscape of QA continues to evolve, organizations must be proactive in exploring new technologies and methodologies to stay competitive and relevant in the market.
- Ultimately, embracing innovation in QA will lead to enhanced product quality and a stronger reputation in the marketplace, making your business a leader in quality assurance.