Table Of Contents
Category
Artificial Intelligence
AIML
Blockchain
1. Introduction
The concept of digital twins has emerged as a revolutionary technology in the realm of digital transformation, reshaping how industries operate, design, and maintain their systems and services. As we delve deeper into the era of the Internet of Things (IoT), artificial intelligence (AI), and machine learning, the role of digital twins has become increasingly significant, offering unprecedented opportunities for innovation and efficiency.
Digital twins serve as a bridge between the physical and digital worlds, providing a dynamic digital representation of physical assets or systems. This technology enables businesses to create, test, and optimize the setups of their systems in a virtual environment before actual physical deployment. This not only reduces the risks and costs associated with physical prototypes but also allows for greater innovation and faster implementation of new ideas.
1.1. Definition of Digital Twins
A digital twin is a virtual model designed to accurately reflect a physical object. The term is predominantly used in the context of industry for replicating processes, products, or services. These digital replicas are continuously updated with data from their physical counterparts, enabling real-time monitoring and simulation of performance. This allows for predictive maintenance, advanced diagnostics, and more efficient operations, which are crucial for modern industries facing complex challenges.
The technology involves the integration of various data sources such as sensors and real-time data analytics to create models that predict how a physical object will perform. By doing so, it provides valuable insights into potential problems and maintenance needs before they occur.
1.2. Importance in Modern Industry
Digital twins are transforming industries by providing detailed insights into product performance, system efficiency, and operational readiness, which in turn helps in optimizing asset management and enhancing operational efficiency. Industries such as manufacturing, automotive, healthcare, and urban planning are already benefiting from this technology. For instance, in manufacturing, digital twins are used to simulate production processes before they are built, to identify potential issues and to improve the efficiency of the production line.
Moreover, the ability to simulate real-world conditions within a virtual environment makes digital twins invaluable for scenario testing without the risk of damaging actual equipment. This aspect is particularly crucial in industries like aerospace and defense, where testing conditions can be extreme and costly. The predictive capabilities of digital twins help in reducing downtime and improving the lifecycle of machinery and equipment, which is a significant advantage in any industry.
For further reading on the importance of digital twins in modern industries, you can explore insights provided by GE Digital on how their digital twin technologies are being implemented across various sectors.
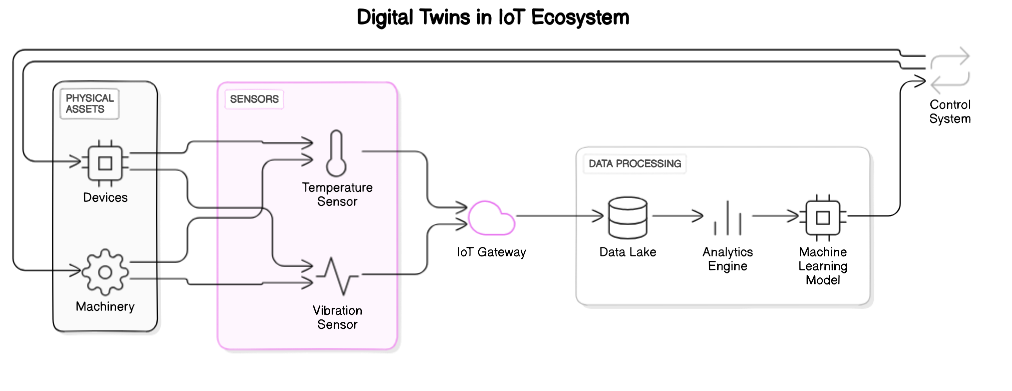
2. How Digital Twins Work
Digital twins function as advanced digital replicas of physical entities, providing a bridge between the physical and digital worlds. This technology integrates internet of things (IoT) sensors, artificial intelligence (AI), machine learning, and software analytics to create living digital simulation models that update and change as their physical counterparts change. A digital twin can be used for various purposes including monitoring, diagnostics, prognostics, and optimized decision-making in real-time across a range of industries such as manufacturing, automotive, healthcare, and urban planning.
The core idea is to gather real-time data from the physical world, which is then used to simulate the object in a digital environment. This simulation can predict how a product or process will perform, thereby helping in making more informed decisions. For instance, in manufacturing, digital twins can predict wear and tear on equipment and suggest maintenance, thus preventing downtime and saving costs.
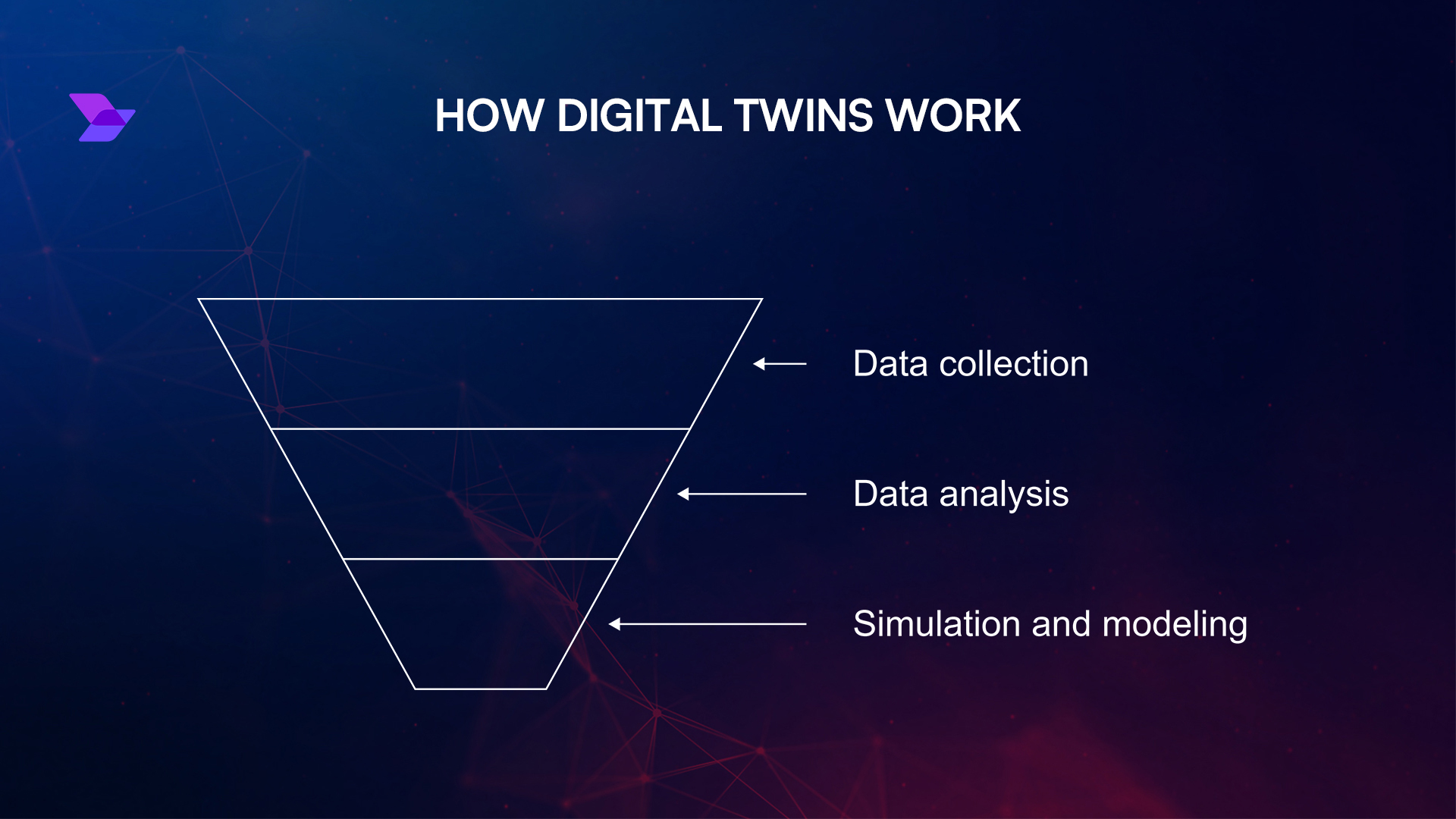
2.1. Data Collection
Data collection is a fundamental step in the functioning of digital twins. It involves deploying sensors and devices to collect data from the physical counterpart. These sensors measure various parameters such as temperature, pressure, humidity, motion, and more, depending on the requirements of the system being monitored. The data collected is comprehensive and continuous, ensuring that the digital twin remains an accurate and up-to-date reflection of the physical object.
The effectiveness of a digital twin heavily relies on the quality and granularity of the data collected. Advanced sensors and IoT devices play a crucial role here, and their development is continuously evolving to provide more precise and real-time data.
2.2. Data Analysis
Once data is collected, the next step is data analysis, which involves processing and interpreting the collected data to make it useful. This process uses various analytical tools and software that apply algorithms and machine learning techniques to identify patterns, detect anomalies, and predict future behavior of the physical counterpart. The outcome of this analysis notifies decision-makers about the health and performance of the physical entity, enabling proactive maintenance and optimization strategies.
Data analysis in digital twins not only helps in understanding current operations but also aids in simulating different scenarios to predict future outcomes. This predictive capability can significantly enhance operational efficiency and innovation.
By continuously analyzing the data, digital twins allow for a dynamic system that adapts and learns over time, thereby providing invaluable insights that drive smarter business decisions.
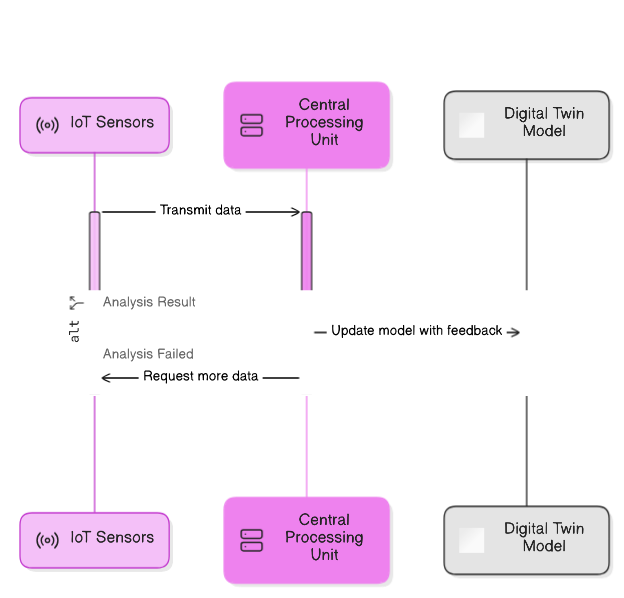
2.3 Simulation and Modeling
Simulation and modeling are essential tools in various fields such as engineering, science, economics, and healthcare. They involve creating digital representations of real-world processes, systems, or events to analyze behavior and predict outcomes in a controlled environment. These tools enable researchers and professionals to experiment with different scenarios and make informed decisions without the risks and costs associated with real-world testing.
For instance, in engineering, simulation and modeling are used to design complex systems like aircraft engines or skyscrapers before actual construction or manufacturing begins. This approach not only saves time and resources but also enhances safety by allowing for thorough testing of designs under various conditions. Similarly, in healthcare, models can predict how a pandemic might spread, which helps in planning and resource allocation to mitigate the impact.
The technology behind simulation and modeling has evolved significantly with advancements in computing power and software development. Tools like MATLAB and Simulink, and platforms such as ANSYS offer sophisticated capabilities for performing detailed simulations and analyzing complex data. These technologies continue to evolve, providing ever more accurate and detailed models that can simulate even the most complex systems and phenomena.
3. What Are Digital Twins?
Digital twins refer to virtual replicas of physical devices, processes, or systems that can be used for various purposes such as simulation, analysis, and monitoring. The concept extends beyond mere simulation, providing a real-time, continuous bridge between the physical and digital worlds. This technology is increasingly used across industries like manufacturing, automotive, healthcare, and urban planning.
The idea is to create a digital counterpart of a physical entity which is dynamically updated with data from sensors and other sources. This allows for real-time monitoring and diagnostics, predictive maintenance, and more efficient operations. For example, in manufacturing, a digital twin of a production line can help in detecting inefficiencies and predicting equipment failures before they occur, thus saving costs and reducing downtime.
The potential of digital twins is vast, with applications ranging from optimizing wind farms to personalizing medical treatments for patients. As the technology matures, it is expected to become standard practice in more industries, helping to drive innovation and efficiency. For more detailed insights, you can visit websites like GE Digital or Siemens, which are pioneers in digital twin technology.
3.1 Core Components
The core components of a digital twin include a physical component, a virtual component, and the connections between them. The physical component is the actual object or system being replicated, such as a jet engine or a building. The virtual component is a dynamic software model that mirrors the physical object in real-time, updated with data from sensors and other sources.
Connectivity is crucial as it facilitates the continuous flow of data between the physical and virtual components. This data can include operational data, environmental conditions, and other relevant metrics that ensure the digital twin remains an accurate and up-to-date reflection of its physical counterpart. Additionally, advanced analytics and machine learning algorithms are often integrated to process this data, enabling predictive maintenance and operational optimizations.
The integration of these components allows for a holistic view of the system’s performance and condition. This integration is supported by technologies such as IoT (Internet of Things), cloud computing, and AI (Artificial Intelligence), which collectively enhance the functionality and utility of digital twins. As these technologies continue to advance, the capabilities of digital twins will expand, leading to more innovative applications and improvements in various industries. For further reading on the technical aspects and applications of digital twins, you might explore resources from IBM or Microsoft, which offer extensive information on the subject.
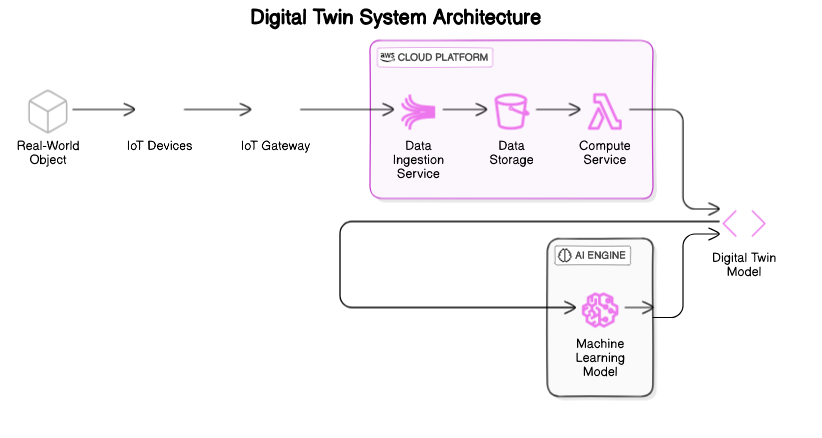
3.2. The Connection with IoT
The Internet of Things (IoT) is fundamentally transforming how we interact with the digital and physical worlds, and one of its most innovative applications is the development of digital twins. A digital twin is a virtual model designed to accurately reflect a physical object. The connection between digital twins and IoT lies in the data. IoT devices collect vast amounts of real-time data from their physical counterparts, which are then used to update and refine the digital twins. This continuous flow of data ensures that the digital twins are up-to-date, providing insights into performance, potential problems, and maintenance needs.
For instance, in industrial settings, sensors can collect data on machine performance and environmental conditions. This data is then mirrored in the digital twin, which can predict when a machine will likely fail or find optimization opportunities for better performance. This integration of IoT with digital twins not only enhances operational efficiency but also reduces downtime and maintenance costs.
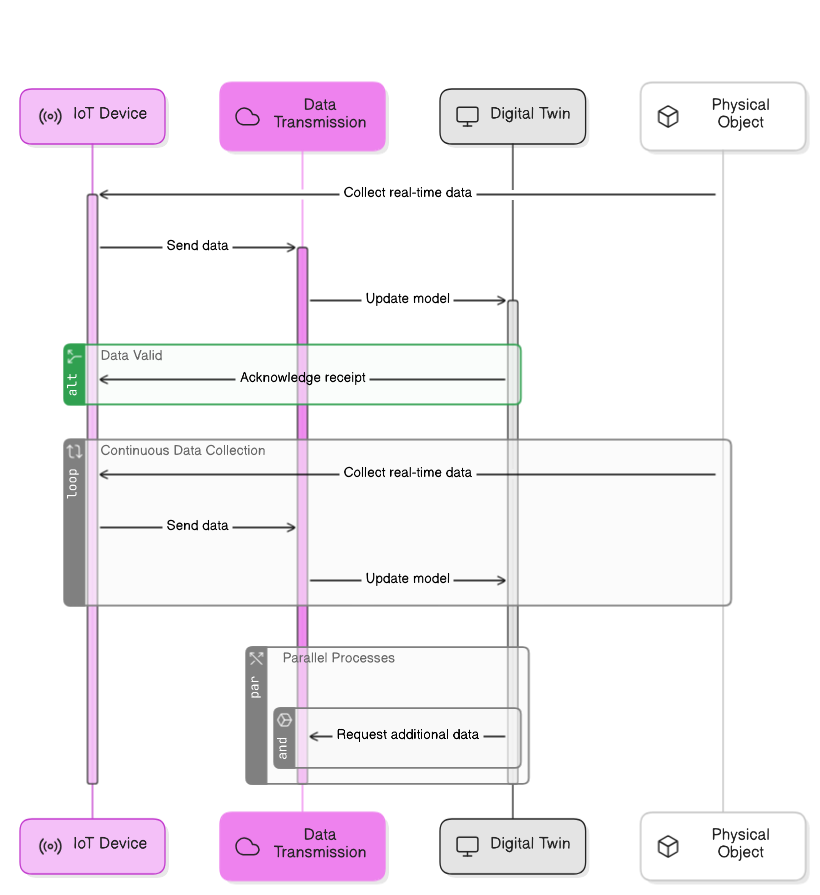
4. Types of Digital Twins
Digital twins can be categorized into several types based on their application and complexity. Understanding these types helps in identifying the right approach for implementing digital twins in various industries and scenarios.

4.1. Product Twins
Product twins are one of the most common types of digital twins, focusing on the lifecycle of a specific product from design to disposal. These twins are used extensively in manufacturing, automotive, aerospace, and consumer goods industries to improve product design, enhance performance, and streamline maintenance processes. By creating a digital replica of a product, engineers can simulate different scenarios and assess the impacts of various design choices without the need for physical prototypes. This not only reduces the time and cost associated with product development but also allows for greater innovation and customization.
Moreover, product twins enable companies to monitor the performance of their products in real-time once they are deployed in the market. This real-time data can lead to proactive maintenance, which significantly enhances customer satisfaction and product reliability. For example, an automotive company might use a product twin to monitor a vehicle's engine performance and predict when maintenance is needed, thereby preventing breakdowns and costly repairs.
4.2. Process Twins
Process Twins are a specific type of digital twin technology that focuses on the simulation, analysis, and optimization of complex processes within various industries. These digital replicas model the sequences of operations in a manufacturing or production process, enabling companies to visualize and predict outcomes with high accuracy, thereby enhancing operational efficiency and reducing downtime.
For instance, in the manufacturing sector, Process Twins can simulate the entire production line to identify bottlenecks or inefficiencies. By analyzing data from sensors and operational metrics, companies can make informed decisions about where to allocate resources, how to minimize waste, and how to improve product quality. This proactive approach to managing production processes can lead to significant cost savings and increased productivity.
4.3. System Twins
System Twins are comprehensive digital replicas that represent the entirety of a system, including all its components and their interactions. This type of digital twin is particularly useful in complex systems like aerospace, automotive, and large-scale manufacturing facilities, where multiple subsystems function together. System Twins help in understanding the overall behavior of these systems under various scenarios, aiding in optimization and innovation.
For example, in the aerospace industry, System Twins can simulate the performance of an entire aircraft under different conditions to predict the outcomes of system modifications or to enhance safety and efficiency. By integrating real-time data from across the system, engineers can troubleshoot issues more effectively and innovate with greater confidence.
5. Benefits of Digital Twins
Digital Twins offer a multitude of benefits across various sectors by providing a bridge between the physical and digital worlds. They enable businesses to create better products, optimize operations, and provide proactive maintenance, ultimately leading to cost reductions and improved efficiency.
One of the primary advantages of Digital Twins is their ability to predict the performance and potential failures of products or systems before they occur. This predictive capability allows companies to take preventive measures, thereby reducing downtime and maintenance costs. Additionally, Digital Twins facilitate more informed decision-making by providing detailed insights into every aspect of the product lifecycle, from design through to disposal.
Moreover, Digital Twins support the customization of products to meet specific customer requirements and help in improving the customer experience. They also play a crucial role in sustainability initiatives by optimizing energy use and reducing waste.
5.1. Enhanced Predictive Maintenance
Predictive maintenance has revolutionized the way industries manage equipment maintenance, shifting from reactive to proactive maintenance strategies. By leveraging data analytics and machine learning, predictive maintenance systems can analyze data from equipment sensors to predict failures before they occur. This approach not only prevents costly downtime but also extends the lifespan of machinery.
For instance, in the manufacturing sector, predictive maintenance can significantly reduce unexpected machine breakdowns. By continuously monitoring equipment conditions, such as vibration, temperature, and power consumption, anomalies can be detected early, allowing maintenance teams to address issues before they lead to equipment failure. This proactive approach is detailed in an article by Deloitte, which discusses how predictive maintenance can lead to a 5-10% reduction in annual maintenance costs, 20-25% reduction in inspection costs, and up to a 70% decrease in breakdowns.
Moreover, industries such as aerospace and transportation also benefit greatly from predictive maintenance. Airlines, for example, use predictive analytics to monitor aircraft engines, predicting failures and scheduling maintenance that doesn’t disrupt flight schedules. This application of predictive maintenance in the aerospace industry is highlighted by the Aviation Industry Corporation of America, which shows how airlines are saving millions annually by avoiding unplanned downtime.
5.2. Improved Product Design and Innovation
The integration of advanced technologies such as AI, IoT, and 3D printing has significantly impacted product design and innovation. These technologies enable designers and engineers to create more efficient, durable, and cost-effective products. For example, AI can simulate countless design scenarios to identify the best materials and structures for specific applications, reducing the time and cost associated with physical prototyping.
In the automotive industry, companies like Tesla are using AI to enhance vehicle design and performance. AI algorithms analyze vast amounts of data from vehicle operations to improve safety features and battery efficiency. This approach not only accelerates the design process but also ensures that the final product meets the highest standards of performance and customer satisfaction.
Similarly, in consumer electronics, companies are using 3D printing to innovate product designs. This technology allows for rapid prototyping, enabling designers to test and refine products quickly. The ability to create complex geometries that were previously impossible to manufacture opens up new possibilities for product innovation. An example of this is seen in how Apple has been rumored to use 3D printing for creating prototypes of new devices, allowing for a faster turnaround from design to production.
5.3. Optimized Operations and Reduced Costs
Optimizing operations and reducing costs are crucial for maintaining competitiveness in any industry. Technologies such as automation, robotics, and advanced analytics play a pivotal role in streamlining operations and minimizing operational costs. Automation, for instance, can handle repetitive tasks more quickly and accurately than human workers, leading to increased productivity and reduced labor costs.
In the retail sector, automation has transformed warehouse operations. Companies like Amazon have implemented sophisticated robotics systems in their fulfillment centers to optimize the picking and packing process, significantly reducing the time it takes to process orders and decreasing operational costs (source: Amazon).
Furthermore, advanced analytics can help businesses optimize their supply chains by predicting market demand and adjusting inventory levels accordingly. This not only prevents overstocking or stockouts but also reduces holding costs. Walmart, for example, uses predictive analytics to fine-tune its inventory management, ensuring that each store has just the right amount of stock based on local demand predictions (source: Walmart).
By integrating these technologies, businesses can achieve a leaner operation, reduce waste, and improve their bottom line, ultimately leading to more sustainable business practices and better customer satisfaction.
6. Challenges in Implementing Digital Twins
Implementing digital twins in industries such as manufacturing, healthcare, and urban planning presents numerous challenges. Digital twins are virtual replicas of physical devices that businesses use to run simulations before actual devices are built and deployed. The technology involves complex systems that require significant investment and management of large data sets, which can pose several challenges.
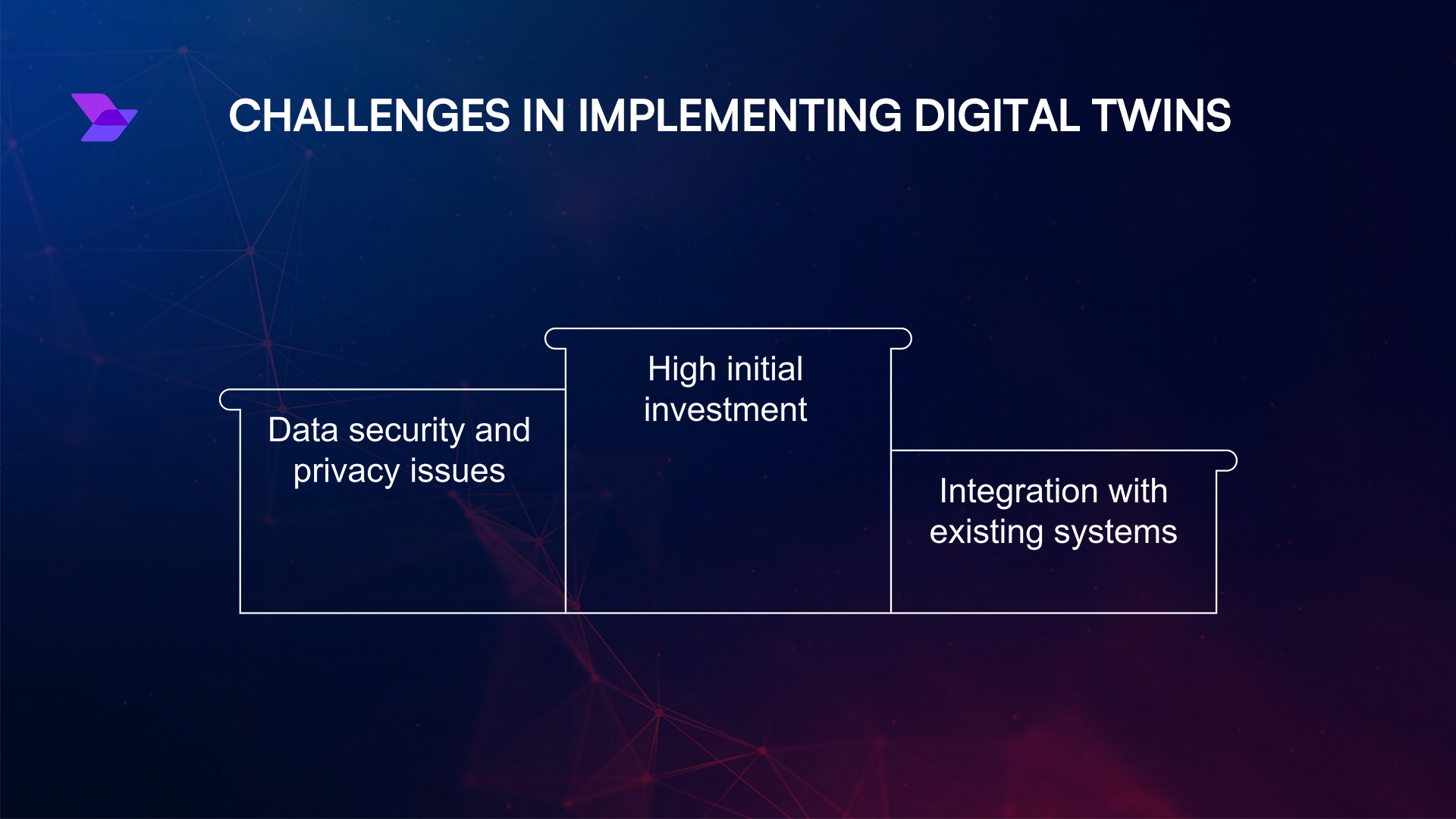
6.1. High Initial Investment
The implementation of digital twins requires substantial initial investment, which can be a significant barrier for many organizations. This investment includes costs related to hardware, such as sensors and other IoT devices, and software, including advanced analytics and simulation tools. Additionally, there is often a need for substantial upgrades to existing IT infrastructure to support the data-intensive nature of digital twin technologies.
The high cost not only encompasses the technological implementation but also the training of personnel and the ongoing maintenance and updating of systems. For many small to medium-sized enterprises (SMEs), these costs can be prohibitive, limiting their ability to adopt this potentially transformative technology. Moreover, the return on investment (ROI) can be uncertain, as the benefits of digital twins may take time to materialize fully.
6.2. Data Security and Privacy Issues
Another significant challenge in implementing digital twins is ensuring data security and privacy. Digital twins rely on a continuous flow of data from their physical counterparts, which often includes sensitive or proprietary information. This data can be vulnerable to cyber-attacks or unauthorized access, which poses a substantial risk to both the integrity of the digital twin system and the privacy of individuals or organizations.
The complexity of digital twin systems, which often integrate data from multiple sources, can make it difficult to ensure all data is securely managed and compliant with relevant data protection regulations, such as GDPR in Europe. Organizations must invest in robust cybersecurity measures and develop comprehensive data governance policies to mitigate these risks.
These challenges highlight the need for careful planning and strategic investment when implementing digital twin technology. Organizations must weigh the potential benefits against the costs and risks to determine if digital twins are a viable solution for their specific needs.
6.3 Integration with Existing Systems
Integrating digital twins with existing systems is a crucial step for organizations aiming to enhance operational efficiency and predictive maintenance capabilities. This integration allows for a seamless flow of data between physical assets and their digital counterparts, enabling real-time monitoring and analysis. For instance, in manufacturing, integrating digital twins with legacy ERP systems can provide insights into production processes, predict equipment failures, and optimize supply chain management.
One of the challenges in integration is ensuring compatibility between new digital twin technologies and older systems that might not have been designed for such advanced analytics. Solutions often involve the use of middleware or customized APIs that facilitate communication between different software applications and hardware systems. IBM offers insights on integrating IoT and AI with existing infrastructures, which can be applied to digital twin technology.
Moreover, the integration process must also consider data security and privacy, especially in industries like healthcare or finance where sensitive data is handled. Ensuring that digital twins do not open new vulnerabilities is paramount.
7. Future of Digital Twins
The future of digital twins is poised to revolutionize various industries by enabling more detailed analysis, predictive maintenance, and enhanced decision-making processes. As these technologies mature, their adoption is expected to grow, leading to more sophisticated and interconnected digital twin ecosystems. Industries such as aerospace, automotive, healthcare, and urban planning are already seeing the benefits of digital twins in optimizing product performance, improving patient outcomes, and enhancing city management.
The ongoing development of digital twins is likely to be significantly influenced by advancements in AI, machine learning, and IoT. These technologies will enable digital twins to not only simulate scenarios but also learn from them, thereby improving their accuracy and utility over time. The integration of digital twins with blockchain could also enhance data security and traceability, a vital aspect as these systems become more prevalent in sensitive areas. For more insights into the future trends and predictions in digital twin technology, Deloitte provides a comprehensive outlook.
7.1 Integration with Advanced Technologies
The integration of digital twins with advanced technologies such as AI, machine learning, and IoT is set to redefine their capabilities and applications. AI and machine learning can process vast amounts of data generated by digital twins to predict outcomes, automate responses, and optimize systems without human intervention. For example, in the automotive industry, digital twins of vehicles can use machine learning to predict when parts will fail or need maintenance, significantly reducing downtime and repair costs.
IoT devices play a critical role in feeding real-time data into digital twins, making them dynamic and responsive. This integration allows for the continuous updating of the digital twin as changes occur in the physical asset, providing a current and accurate reflection at all times. The potential for IoT to expand the capabilities of digital twins is explored in detail by Cisco in their analysis of IoT data management.
Furthermore, the integration with other emerging technologies like augmented reality (AR) and virtual reality (VR) can enhance the visualization and interaction with digital twins. This can be particularly useful in training, maintenance, and troubleshooting scenarios, where immersive simulations can provide hands-on experience without the associated risks or costs. The convergence of these advanced technologies promises to not only expand the scope of digital twins but also increase their effectiveness and accessibility across different sectors.
7.2. Broader Industry Adoption
Digital twins, once a novel concept, are now seeing broader adoption across various industries, revolutionizing how businesses operate and innovate. This technology, which involves creating digital replicas of physical assets, systems, or processes, allows for real-time monitoring, simulation, and analysis. Industries such as manufacturing, automotive, healthcare, and even urban planning are leveraging digital twins to optimize operations, enhance product development, and improve services.
In manufacturing, digital twins are used to create and simulate factory settings before physical plants are built, allowing companies to optimize layouts and processes without the high costs associated with physical prototyping. Companies like Siemens and General Electric have been pioneers in this area, integrating digital twin technology into their operations to predict maintenance issues and improve production efficiency. For more detailed insights into how these companies are utilizing digital twins, you can visit their official websites or dedicated technology sections.
The automotive industry is another area where digital twins are becoming increasingly integral. Car manufacturers are using digital twins to simulate vehicle performance under various conditions, thereby enhancing design and safety features before the vehicle hits the road. This not only reduces the time and cost associated with physical testing but also allows for a more in-depth analysis of potential issues.
Healthcare is also beginning to see the benefits of digital twin technology. Hospitals and health systems use digital twins to simulate patient flows and optimize hospital operations, which can lead to better patient outcomes and more efficient use of resources. This application of digital twins in healthcare is detailed further in articles and case studies available on healthcare technology news platforms.
7.3. Evolution of Standards and Regulations
As digital twin technology becomes more prevalent, the evolution of standards and regulations is crucial to ensure its effective and safe implementation. Standardization bodies and regulatory agencies are working to establish frameworks that address data security, privacy, interoperability, and ethical considerations associated with digital twins. These standards are essential for fostering innovation while ensuring that the technology is used responsibly and effectively across different sectors.
Organizations such as the International Organization for Standardization (ISO) and the National Institute of Standards and Technology (NIST) are at the forefront of developing these standards. They focus on creating guidelines that ensure digital twins are built and operated in a way that is secure and interoperable with other systems and technologies. For more information on the latest standards and regulations, visiting the websites of these organizations can provide valuable resources and updates.
In addition to technical standards, there is also a growing focus on the ethical implications of digital twins, particularly in terms of data privacy and the potential for misuse of personal data. Regulatory bodies in various countries are beginning to draft legislation that addresses these concerns, aiming to protect individuals and organizations while promoting the growth of digital twin technologies.
8. Real-World Examples of Digital Twins
Real-world applications of digital twins are demonstrating their potential across diverse sectors. One notable example is Singapore’s virtual twin of the entire city, used for urban planning and environmental simulations. This digital twin helps city planners manage everything from traffic systems to disaster responses, providing a powerful tool for sustainable urban development. More details on this project can be found on Singapore's official urban planning websites.
In the energy sector, BP uses digital twins to simulate drilling and refining processes, which helps in optimizing operations and reducing downtime. By predicting equipment failures before they occur, BP can conduct maintenance proactively, significantly reducing operational costs and enhancing safety. The specifics of BP’s use of digital twins can be explored further through their corporate publications and energy industry reports.
Another compelling example is found in aerospace, where NASA employs digital twins to monitor and simulate spacecraft conditions to predict potential system failures before they happen. This application not only improves mission safety but also enhances the overall efficiency of space operations. Detailed case studies and reports on NASA’s use of digital twins are available through aerospace technology forums and NASA’s own digital platforms.
These examples illustrate just a few of the ways digital twins are being used to transform industries by providing detailed insights and predictive capabilities that were not possible before.
8.1. Manufacturing: Aerospace and Automotive
The manufacturing sector, particularly in aerospace and automotive industries, has been revolutionized by advancements in technology and production methodologies. In aerospace, manufacturers are leveraging cutting-edge technologies such as 3D printing to create lighter and more complex components that contribute to the efficiency and sustainability of aircraft. For instance, GE Aviation has developed advanced turbine blades using 3D printing technology, which are not only lighter but also more durable than traditional blades. More details on this can be found on GE Aviation’s official website.
In the automotive sector, the integration of automation and IoT (Internet of Things) has transformed production lines, making them smarter and more efficient. Companies like Tesla have pioneered the use of high automation in car manufacturing, significantly reducing human error and increasing production speed. The use of robotics in assembly lines, as detailed in a report by McKinsey, has led to a decrease in production costs and an improvement in the quality of vehicles.
Furthermore, both industries are increasingly focusing on sustainability, with efforts to reduce carbon footprints and waste during the manufacturing process. The adoption of electric vehicles (EVs) and the development of sustainable aviation fuels are prominent examples of how these sectors are addressing environmental concerns. More information on sustainability practices in these industries can be found on the Environmental Protection Agency’s website.
8.2. Healthcare: Personalized Medicine and Prosthetics
Healthcare has seen significant transformations with the advent of personalized medicine and advancements in prosthetics. Personalized medicine, or precision medicine, tailors medical treatment to the individual characteristics of each patient, which can dramatically increase the efficacy of treatments and reduce side effects. This approach uses genetic information to guide decisions made in the prevention, diagnosis, and treatment of diseases. The National Institutes of Health (NIH) provides a comprehensive resource on how personalized medicine is being integrated into healthcare.
Prosthetics have also undergone considerable innovation, with the development of bionic limbs that offer greater functionality and comfort to amputees. These advanced prosthetic limbs are now equipped with sensors that mimic the natural movement of human limbs, significantly improving the quality of life for users. Companies like Ottobock and research from institutions such as MIT are at the forefront of these developments, pushing the boundaries of what is possible in prosthetic technology.
Moreover, the integration of AI and machine learning in healthcare practices is helping in the early detection of diseases and the management of chronic conditions, with systems able to analyze data and recognize patterns that may not be apparent to human observers. This technological integration is paving the way for more proactive and preventive healthcare approaches.
8.3. Smart Cities: Urban Planning and Management
Smart cities use digital technology to enhance performance and well-being, to reduce costs and resource consumption, and to engage more effectively and actively with their citizens. Key aspects of smart cities include urban planning and management, where technology is used to improve infrastructure efficiency and enhance the quality of life. The use of IoT devices in urban areas for monitoring traffic, air quality, and energy use helps city planners manage everything more effectively and sustainably. The Smart Cities Council provides examples of how cities around the world are implementing these technologies.
Urban planning also benefits from the use of big data and AI to predict urban growth and to optimize public transport routes and schedules. For instance, cities like Singapore have implemented dynamic public transport systems that adjust to real-time data to improve efficiency and reduce congestion. Further insights into these implementations can be found on Singapore’s Urban Redevelopment Authority website.
Moreover, smart city initiatives also focus on improving the resilience of urban areas to environmental challenges and emergencies. Technologies like automated flood defenses and earthquake-resistant infrastructures are becoming integral parts of urban planning. The integration of green spaces and sustainable materials in building designs is also a focus area, aiming to create not only smarter but also greener cities.
Each of these points highlights how technology is not just enhancing efficiency but also pushing the boundaries of what is possible in manufacturing, healthcare, and urban management, leading to more sustainable and improved practices across these sectors.
9. In-Depth Explanations
9.1. The Role of AI and Machine Learning
Artificial Intelligence (AI) and Machine Learning (ML) are rapidly transforming industries by automating complex processes, enhancing data analysis, and improving decision-making. AI refers to the simulation of human intelligence in machines that are programmed to think like humans and mimic their actions. Machine Learning, a subset of AI, involves the development of algorithms that allow computers to learn from and make predictions or decisions based on data.
The integration of AI and ML in various sectors such as healthcare, finance, and automotive has led to significant advancements. In healthcare, AI-powered tools can analyze medical images with greater accuracy than human radiologists, leading to earlier and more precise diagnoses. For instance, AI algorithms are used to detect anomalies in X-ray and MRI scans that could be indicative of diseases like cancer. In the financial sector, ML models are employed to detect fraudulent activities by recognizing patterns in transaction data that are typically associated with fraud.
Moreover, AI and ML are pivotal in the development of autonomous vehicles. These technologies process vast amounts of data from vehicle sensors and external sources to make real-time decisions, enhancing road safety and reducing human error. The future of AI and ML promises even more personalized services, smarter business operations, and innovative solutions to complex problems.
9.2. The Impact of Blockchain Technology
Blockchain technology, best known as the backbone of cryptocurrencies like Bitcoin, is a decentralized digital ledger that records transactions across multiple computers. Its impact extends far beyond cryptocurrencies, influencing sectors such as supply chain management, healthcare, and finance by offering enhanced security, transparency, and efficiency.
In supply chain management, blockchain provides an immutable record of product journeys from manufacture to sale, helping to prevent fraud and ensuring compliance with safety standards. It enables all parties in the supply chain to access the same information, potentially reducing disputes and delays. For example, Walmart uses blockchain to track the origin of produce and meat, significantly reducing the time it takes to trace the source of food items from days to seconds.
In the financial sector, blockchain technology disrupts traditional banking by facilitating faster and more secure transactions. It eliminates the need for intermediaries like banks, reducing transaction costs and increasing processing speed. Moreover, blockchain's potential in creating "smart contracts" automates and enforces contracts between parties, reducing the need for legal intermediaries and making transactions more straightforward.
The healthcare sector also benefits from blockchain by enhancing the security and interoperability of medical records. It allows for secure sharing of patient data between providers, which can improve treatment outcomes and patient care efficiency. As blockchain technology continues to evolve, its potential to revolutionize various industries by providing secure, transparent, and efficient solutions is immense.
10. Comparisons & Contrasts
10.1. Digital Twins vs. Traditional Simulation Models
Digital twins and traditional simulation models are both valuable tools in the realm of engineering and design, but they serve different purposes and operate in distinct ways. A digital twin is a virtual model of a process, product, or service. This pairing of the virtual and physical worlds allows for data analysis and system monitoring to prevent problems before they even occur, prevent downtime, develop new opportunities, and even plan for the future by using simulations.
On the other hand, traditional simulation models typically focus on specific aspects of a system or process, often without continuous real-time data updates. These models are generally static, representing systems at a particular point in time. While traditional simulations are excellent for hypothesis testing and scenario analysis, they lack the dynamic adaptability provided by digital twins, which can continuously learn and update from ongoing data.
The key difference lies in their application and functionality. Digital twins offer a dynamic and more holistic approach, integrating IoT (Internet of Things) technologies to create live simulations that update and change along with their real-world counterparts. Traditional models, while still useful, do not dynamically interact with real-world data, which can limit their effectiveness in applications where conditions change rapidly.
10.2. Digital Twins in Different Industries
The application of digital twins spans across various industries, each leveraging this technology to solve unique challenges and improve efficiency. In manufacturing, digital twins are used to create replicas of production lines to optimize operations and predict maintenance issues before they cause downtime. The automotive industry uses digital twins for everything from the design and testing of new vehicle models to the analysis of supply chains and production processes.
In the healthcare sector, digital twins are revolutionizing patient care by creating personalized medical treatments and advanced diagnostics. Hospitals use digital twins to simulate the impacts of surgical interventions on patients before actual procedures, enhancing the precision and safety of medical care. The energy sector benefits from digital twins in optimizing the performance of assets and systems, from wind turbines to entire power grids, thus enhancing energy efficiency and reliability.
The versatility of digital twins demonstrates their potential to transform traditional business models and operational processes across different sectors. Each industry adopts this technology in ways that best suit their specific needs and challenges, leading to widespread innovation and efficiency improvements.
11. Why Choose Rapid Innovation for Implementation and Development
Choosing Rapid Innovation for your implementation and development needs can significantly enhance your business's ability to adapt to new technologies and market demands efficiently. Rapid Innovation, as a concept, focuses on quickly integrating cutting-edge technologies and methodologies to drive business growth and maintain competitive advantage. This approach is particularly crucial in today’s fast-paced digital landscape where technological advancements occur at an exponential rate.
By adopting Rapid Innovation, companies can reduce the time it takes to go from concept to deployment, which is vital for capitalizing on new opportunities and addressing challenges effectively. This strategy not only speeds up the process of innovation but also encourages a more agile and responsive organizational culture. Moreover, it allows businesses to test and refine their innovations in real-time, ensuring that the final products or services are well-optimized and market-ready.
11.1. Expertise in AI and Blockchain
Rapid Innovation often involves leveraging advanced technologies such as Artificial Intelligence (AI) and Blockchain, which are pivotal in transforming industries across various sectors. Companies like Rapid Innovation bring deep expertise in these areas, providing tailored solutions that integrate these technologies to solve complex business problems and enhance operational efficiencies.
AI and Blockchain are particularly notable for their potential to automate processes, secure data transactions, and provide new insights through data analytics. For instance, AI can be used to predict customer behavior, optimize logistics, and improve decision-making processes, while Blockchain offers unparalleled security features for transactions and can significantly reduce costs and improve transparency in supply chains.
Experts in these technologies can help businesses implement solutions that are not only innovative but also aligned with industry standards and regulatory requirements, ensuring a smooth and successful integration into existing systems.
11.2. Proven Track Record
Choosing a partner with a proven track record in Rapid Innovation ensures that you are working with a team that has successfully navigated the complexities of implementing new technologies in a real-world setting. Such companies have demonstrated their ability to deliver projects on time and within budget while achieving the desired outcomes for their clients.
A proven track record also indicates that the company has refined its methodologies and processes over time, learning from past projects and continuously improving its approach to innovation. This experience is invaluable as it reduces the risk associated with new technology implementations and ensures that the solutions provided are both effective and sustainable.
Moreover, companies with a proven track record in Rapid Innovation are likely to have established strong relationships with technology providers, industry experts, and other stakeholders, which can provide additional resources and support for your projects. This network can be crucial in navigating the challenges of innovation and ensuring that your company remains at the forefront of technological advancements.
11.3 Customized Solutions
Customized solutions in various industries signify a shift from one-size-fits-all to more tailored, client-specific strategies that address unique challenges and requirements. This approach is particularly beneficial in sectors like healthcare, IT, and marketing, where customization can lead to significantly improved outcomes. For instance, in healthcare, personalized treatment plans based on genetic information have become more prevalent, offering more effective care tailored to individual genetic profiles.
In the realm of information technology, customized software solutions allow businesses to enhance efficiency by addressing specific operational needs. This could range from custom CRM systems designed to fit the unique sales processes of a company, to specialized logistics software that optimizes supply chain operations for a particular market niche. Websites like Salesforce provide extensive insights on how customized CRM systems can boost customer satisfaction and operational efficiency (https://www.salesforce.com).
Moreover, in marketing, the customization of campaigns and communications allows companies to engage more effectively with diverse market segments. Tailored marketing messages based on consumer behavior and preferences increase engagement rates and conversion, as detailed in various case studies available on HubSpot (https://www.hubspot.com).
12. Conclusion
In conclusion, embracing the digital transformation and its components like AI, IoT, and customized solutions is no longer optional for businesses aiming to remain competitive in a rapidly evolving market landscape. These technologies not only enhance operational efficiencies but also improve customer engagement and open new avenues for innovation.
12.1 Summary of Key Points
To summarize, the key points discussed highlight the importance of integrating advanced technologies such as AI and IoT in modern business practices. AI's role in automating complex processes and deriving insights from large datasets has been transformative across various sectors. Similarly, IoT's contribution to enhancing connectivity and real-time data exchange has revolutionized operations, particularly in industries like manufacturing and logistics.
The discussion also emphasized the significance of customized solutions, which cater to specific business needs and customer preferences, thereby enhancing efficiency and effectiveness in service delivery. The ability to tailor products, services, and communications to meet the unique demands of each client or market segment is a critical competitive advantage in today's business environment.
In essence, the integration of these technologies and approaches is crucial for businesses seeking to innovate, improve customer satisfaction, and increase operational efficiencies in the digital age.
12.2 The Strategic Importance of Digital Twins
Digital twins are virtual replicas of physical devices that data scientists and IT pros can use to run simulations before actual devices are built and deployed. The strategic importance of digital twins lies in their ability to improve the understanding of products and processes, optimize business operations, and drive innovation. By integrating IoT, AI, machine learning, and analytics, digital twins offer a powerful tool for businesses across various industries, including manufacturing, healthcare, automotive, and urban planning.
One of the primary strategic advantages of digital twins is their role in enhancing product development and operational efficiency. By creating a digital twin of a product or system, companies can test and analyze how it will perform under different conditions without the need to build multiple prototypes. This not only reduces the time and cost associated with product development but also allows for the optimization of the product design for better performance and reliability. For instance, in the automotive industry, digital twins are used to simulate vehicle dynamics under various conditions to improve safety and efficiency before the vehicle hits the market.
Furthermore, digital twins facilitate predictive maintenance, which can significantly reduce downtime and maintenance costs. By continuously monitoring the condition and performance of physical assets through their digital counterparts, companies can predict when a machine will likely fail and perform maintenance proactively. This approach helps in avoiding unexpected breakdowns and prolonging the lifespan of the equipment.
In addition to operational efficiencies, digital twins also play a crucial role in strategic planning and decision-making. They provide valuable insights that can help businesses anticipate market changes, adapt to new regulations, and improve customer satisfaction. For example, in urban planning, digital twins can simulate the impact of new policies or infrastructure changes on traffic patterns and public safety, helping city planners make informed decisions.